Zero-thrust multifunctional rotating compensator and manufacturing method thereof
A rotary compensator, multi-functional technology, applied in the expansion compensation device, adjustable connection, passing element and other directions of pipelines, can solve the problems of increasing rotation resistance, pipeline thermal loss, affecting economic benefits, etc., to achieve enhanced sealing effect , prolong the service life, save energy and protect the environment
- Summary
- Abstract
- Description
- Claims
- Application Information
AI Technical Summary
Problems solved by technology
Method used
Image
Examples
Embodiment Construction
[0026] Below in conjunction with accompanying drawing and specific embodiment the present invention will be further described:
[0027] Such as figure 1 As shown, the non-thrust multifunctional rotary compensator includes a rotary tube 1 and a rotary seat 3, one end of the rotary seat 3 is provided with a rotary seat flange 31, and the rotary tube 1 is sleeved in the rotary seat 3, and the rotary seat 3 The other end is provided with an arc-shaped contraction tube B, the side of the rotary seat flange 31 is provided with a packing gland flange 2, the outer circumference of the rotary tube 1 is provided with a rotary tube convex ring 12, and the inner wall of the rotary seat 3 is provided with a packing ring 33 , the stuffing gland flange 2, the rotating pipe convex ring 12 and the rotating seat 3 constitute the first packing chamber 4, the rotating pipe convex ring 12 and the packing ring 33 of the rotating seat 3 constitute the second packing chamber 5, and the rotating pipe ...
PUM
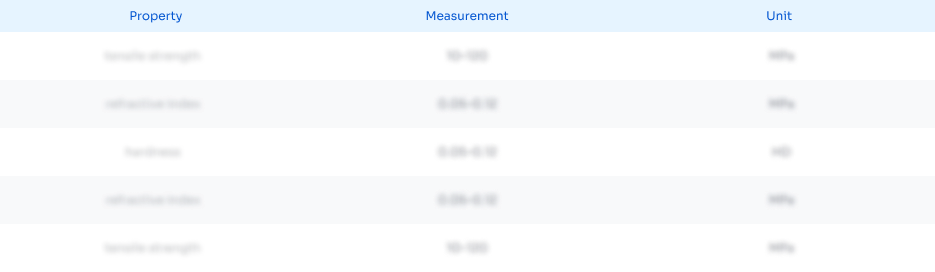
Abstract
Description
Claims
Application Information

- Generate Ideas
- Intellectual Property
- Life Sciences
- Materials
- Tech Scout
- Unparalleled Data Quality
- Higher Quality Content
- 60% Fewer Hallucinations
Browse by: Latest US Patents, China's latest patents, Technical Efficacy Thesaurus, Application Domain, Technology Topic, Popular Technical Reports.
© 2025 PatSnap. All rights reserved.Legal|Privacy policy|Modern Slavery Act Transparency Statement|Sitemap|About US| Contact US: help@patsnap.com