Precast steel pipe concrete laminated column
A technology of steel tube concrete and laminated columns, which is applied in the direction of columns, pier columns, pillars, etc., can solve the problems of environmental pollution, construction noise, inability of concrete and surrounding concrete to bear force and deformation coordination, and long construction time of cast-in-place concrete. Small impact on the environment, beneficial to environmental protection, and superior seismic performance
- Summary
- Abstract
- Description
- Claims
- Application Information
AI Technical Summary
Problems solved by technology
Method used
Image
Examples
Embodiment 1
[0063] Such as figure 1As shown, a prefabricated steel tube concrete composite column includes a foundation and a plurality of steel tube concrete segments, and the multiple steel tube concrete segments include a bottom segment, a top segment and one or more intermediate segments of steel tube concrete Segments, each CFST segment includes a lower steel plate, a CFST main body, and an upper steel plate that are fixedly connected sequentially from bottom to top. Concrete is injected inside, and the upper and lower steel plates between the bottom segment and the middle segment and between the middle segment and the top segment are respectively provided with connecting anchor bolts or connecting holes so that the adjacent upper and lower steel plates The connection is fixed by means of connecting anchor bolts. The upper steel plate is provided with pouring holes at the positions corresponding to the top openings of the steel pipes. The pouring holes are used to pour concrete when ...
Embodiment 2
[0086] In this embodiment, on the basis of Embodiment 1, the shear connector is designed as a steel plate with holes, and the steel plate with holes is a strip-shaped steel plate 29, such as Figure 10 As shown, the strip-shaped steel plate 29 is provided with through holes 24 at equal intervals. The setting of the through hole 24 is beneficial to strengthen the connection between the shear connector and the concrete, and improve the ability of working together and coordinating deformation. Such as Figure 11 As shown, the shear connector 15 is configured as a strip-shaped steel plate 29 that can be welded vertically inside and outside the steel pipe 19 . Different strip-shaped steel plates 29 are arranged parallel to each other and arranged at intervals inside and outside the steel pipe 19 . Further, steel bars can be arranged in the holes for a better connection. Specifically, steel bars are penetrated in the through holes of the perforated steel plates at the same horizont...
PUM
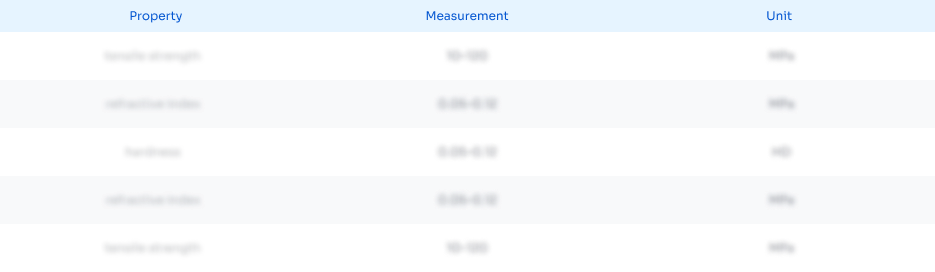
Abstract
Description
Claims
Application Information

- R&D
- Intellectual Property
- Life Sciences
- Materials
- Tech Scout
- Unparalleled Data Quality
- Higher Quality Content
- 60% Fewer Hallucinations
Browse by: Latest US Patents, China's latest patents, Technical Efficacy Thesaurus, Application Domain, Technology Topic, Popular Technical Reports.
© 2025 PatSnap. All rights reserved.Legal|Privacy policy|Modern Slavery Act Transparency Statement|Sitemap|About US| Contact US: help@patsnap.com