Efficient and high-precise robot automatic milling system in digital assembly process of airplane
An automatic milling and robot technology, applied in the direction of manipulators, positioning devices, maintenance and safety accessories, etc., can solve the problems of uneven allowance, difficult repair, low work efficiency, etc., and achieve reduced labor intensity, high reliability, and improved assembly The effect of precision
- Summary
- Abstract
- Description
- Claims
- Application Information
AI Technical Summary
Problems solved by technology
Method used
Image
Examples
Embodiment 1
[0045] The specific processing process of aircraft large parts is as follows:
[0046] Step 1: The laser tracker scans the feature points of the front fuselage and the middle fuselage to be assembled, establishes a global coordinate system, and transmits the global coordinate system information to the measurement system 6 through an interface;
[0047] Step 2: The measurement system 6 is placed on the measurement system quick-change bracket 24, the coordinate tracking system 61 tracks the scanning head of the scanning system 62 in real time, and places 4~ 5 target balls are ready for posture correction;
[0048] Step 3: Control the AGV trolley 1 to enter the first station in the processing area (the processing robot 42 enters first, and the center of the processing robot base 41 is consistent with the central axis of the machine head to be processed) and anchored;
[0049] Step 4: The processing robot 42 is assembled with the measurement system 6, and the scanning system 62 s...
Embodiment 2
[0065] The specific processing process of aircraft small parts is as follows:
[0066] Step 1: Determine the layout of the vacuum chucks 74 according to the range projected onto the flexible positioning tooling system 3 by the mouth cover. After fixing each vacuum chuck 74, determine the horizontal plane coordinates of each vacuum chuck 74 relative to the tooling reference point with a measuring ruler ;
[0067] Step 2: Import the theoretical digital model of the flap into the GeoMagic software for simulation calculation, and calculate each vacuum sucker in the flexible positioning tooling system 3 according to the theoretical digital model of the flap and the distribution of each vacuum sucker 74 relative to the reference point of the tooling 74 telescoping height;
[0068] Step 3: adjust the height of each vacuum suction cup 74;
[0069] Step 4: Correspond the datum point of the mouth cover with the datum point of the tooling, and fix it on the flexible positioning tooling...
PUM
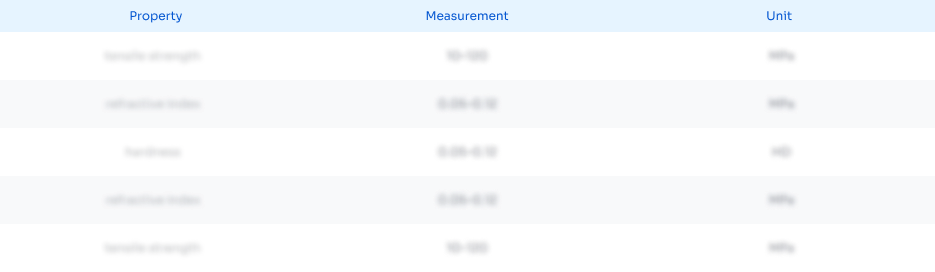
Abstract
Description
Claims
Application Information

- R&D
- Intellectual Property
- Life Sciences
- Materials
- Tech Scout
- Unparalleled Data Quality
- Higher Quality Content
- 60% Fewer Hallucinations
Browse by: Latest US Patents, China's latest patents, Technical Efficacy Thesaurus, Application Domain, Technology Topic, Popular Technical Reports.
© 2025 PatSnap. All rights reserved.Legal|Privacy policy|Modern Slavery Act Transparency Statement|Sitemap|About US| Contact US: help@patsnap.com