Method for smooth and steady floating and descending of moving-coil permanent magnetic planar motor, without position sensor
A permanent magnet plane, moving coil technology, applied to holding devices, instruments, electrical components, etc. using magnetic attraction or thrust, can solve the problems of complex programming, long positioning time, position jitter, etc., to reduce execution errors. , The effect of short positioning time and cost saving
- Summary
- Abstract
- Description
- Claims
- Application Information
AI Technical Summary
Problems solved by technology
Method used
Image
Examples
Embodiment Construction
[0021] Below with reference to accompanying drawing, through the description of embodiment, the specific embodiment of the present invention such as the shape of each component involved, structure, mutual position and connection relationship between each part, the effect of each part and working principle, manufacturing process And the method of operation and use, etc., are described in further detail to help those skilled in the art have a more complete, accurate and in-depth understanding of the inventive concepts and technical solutions of the present invention.
[0022] figure 1 It is a simplified structure diagram of the moving coil permanent magnet planar motor. The coordinate system setting, stator permanent magnet array layout, and mover coil array layout are shown in the figure. The moving coil permanent magnet planar motor is mainly divided into two parts: the stator and the mover. The stator is composed of a two-dimensional Halbach permanent magnet array, which con...
PUM
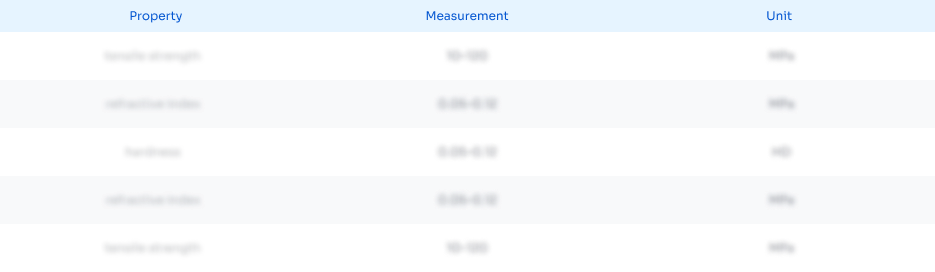
Abstract
Description
Claims
Application Information

- R&D
- Intellectual Property
- Life Sciences
- Materials
- Tech Scout
- Unparalleled Data Quality
- Higher Quality Content
- 60% Fewer Hallucinations
Browse by: Latest US Patents, China's latest patents, Technical Efficacy Thesaurus, Application Domain, Technology Topic, Popular Technical Reports.
© 2025 PatSnap. All rights reserved.Legal|Privacy policy|Modern Slavery Act Transparency Statement|Sitemap|About US| Contact US: help@patsnap.com