Sieve hole built-in type annular laser cladding nozzle
A laser cladding, conical nozzle technology, applied in the direction of metal material coating process, coating, etc., can solve the problems of surface deterioration of formed parts, poor powder flow uniformity, burnt nozzle and other problems, to improve convergence, good powder Light-matching, easy-to-replace effects
- Summary
- Abstract
- Description
- Claims
- Application Information
AI Technical Summary
Problems solved by technology
Method used
Image
Examples
Embodiment Construction
[0025] The present invention will be further explained below in conjunction with the accompanying drawings.
[0026] Such as figure 1 As shown, a built-in sieve ring laser cladding nozzle of the present invention includes a laser head connection part, a middle sleeve part and a nozzle part.
[0027] The laser head connection part includes an upper connection sleeve 1, the upper end of the upper connection sleeve 1 is connected with the laser head, and the laser cladding nozzle of the present invention is connected with the laser equipment through the upper connection sleeve 1.
[0028] The middle sleeve part includes a sliding sleeve 3 , a protective glass water cooling jacket 4 , a central sleeve 16 and a protective glass 20 . The upper end of the sliding sleeve 3 is connected to the lower end of the upper connecting sleeve 1. In this embodiment, the upper end of the sliding sleeve 3 extends into the connecting sleeve 1 and can slide up and down along the connecting sleeve 1...
PUM
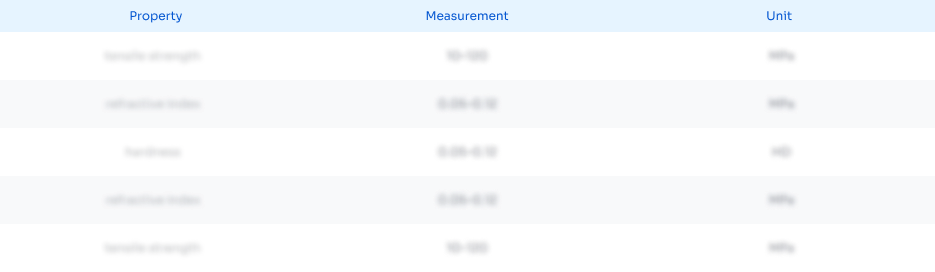
Abstract
Description
Claims
Application Information

- R&D Engineer
- R&D Manager
- IP Professional
- Industry Leading Data Capabilities
- Powerful AI technology
- Patent DNA Extraction
Browse by: Latest US Patents, China's latest patents, Technical Efficacy Thesaurus, Application Domain, Technology Topic, Popular Technical Reports.
© 2024 PatSnap. All rights reserved.Legal|Privacy policy|Modern Slavery Act Transparency Statement|Sitemap|About US| Contact US: help@patsnap.com