A method for rapidly preparing silver nanosquare-graphene-nickel foam composites
A composite material and graphene technology, applied in the direction of graphene, nano-carbon, etc., can solve the problems of poor electrical conductivity, poor mechanical properties, difficulty in recycling, and long time consumption, so as to achieve improved mechanical properties, convenient operation, and reduced The effect of the transfer process
- Summary
- Abstract
- Description
- Claims
- Application Information
AI Technical Summary
Problems solved by technology
Method used
Examples
Embodiment 1
[0027] 1) Preparation of graphene-nickel foam by CVD method: the nickel foam was cleaned with acetone, ethanol, and deionized water for 15-20 min respectively to remove the surface oxide layer, and then washed with N 2 Blow dry; put it into the furnace quartz tube to evacuate, remove the air in the tube, and pass in Ar and H 2 , during the annealing process, the Ar flow rate is 100 sccm, and the H 2 The flow rate is 20sccm, the temperature is raised to 900°C at a rate of 15°C / min, and annealed at this temperature for 30min; when growing graphene, CH 4 and H 2 , the graphene growth process leads to CH 4 The flow rate is 10sccm, and H 2 Flow rate is 50sccm, grow for 5min; disconnect CH after growth 4 , and quickly lower the temperature, and take out the sample after the furnace cools down to room temperature, and obtain a nickel foam material covered with graphene.
[0028] 2) Preparation of silver nanocube: fix the cleaned three-neck flask in an oil bath at 140°C, put in a...
Embodiment 2
[0031] 1) Preparation of graphene-nickel foam by CVD method: wash the nickel foam with acetone, ethanol, and deionized water for 15-20 minutes respectively to remove the surface oxide layer, and then blow dry with N2; put it into the furnace quartz tube to evacuate, and remove The air in the tube is fed with Ar and H 2 , during the annealing process, the Ar flow rate is 110sccm, and the H 2 The flow rate is 30sccm, the temperature is raised to 930°C at a rate of 15°C / min, and annealed at this temperature for 33min; CH is introduced when growing graphene 4 and H 2 , the graphene growth process leads to CH 4 The flow rate is 11sccm, and H 2 Flow rate is 60sccm, grow for 5min; disconnect CH after growth 4 , and quickly lower the temperature, and take out the sample after the furnace cools down to room temperature, and obtain a nickel foam material covered with graphene.
[0032] 2) Preparation of silver nanocube: fix the cleaned three-neck flask in an oil bath at 150°C, put ...
Embodiment 3
[0035] 1) Preparation of graphene-nickel foam by CVD method: the nickel foam was cleaned with acetone, ethanol, and deionized water for 15-20 min respectively to remove the surface oxide layer, and then washed with N 2 Blow dry; put it into the furnace quartz tube to evacuate, remove the air in the tube, and pass in Ar and H 2 , during the annealing process, the Ar flow rate is 120sccm, and the H 2 The flow rate is 40sccm, the temperature is raised to 960°C at a rate of 15°C / min, and annealed at this temperature for 36min; CH is introduced when growing graphene 4 and H 2 , the graphene growth process leads to CH 4 The flow rate is 12sccm, and H 2 Flow rate is 70sccm, grow for 5min; disconnect CH after growth 4 , and quickly lower the temperature, and take out the sample after the furnace cools down to room temperature, and obtain a nickel foam material covered with graphene.
[0036] 2) Preparation of silver nanocube: fix the cleaned three-neck flask in an oil bath at 160...
PUM
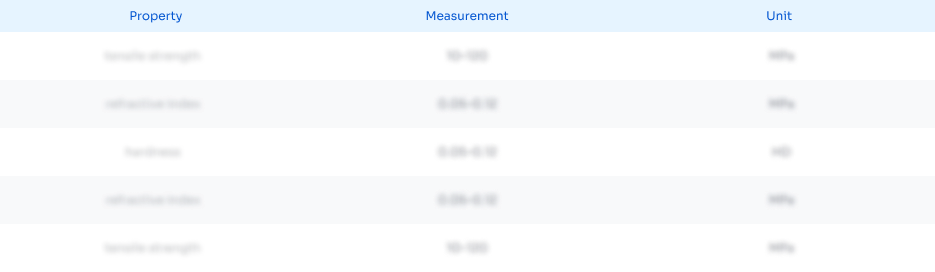
Abstract
Description
Claims
Application Information

- R&D
- Intellectual Property
- Life Sciences
- Materials
- Tech Scout
- Unparalleled Data Quality
- Higher Quality Content
- 60% Fewer Hallucinations
Browse by: Latest US Patents, China's latest patents, Technical Efficacy Thesaurus, Application Domain, Technology Topic, Popular Technical Reports.
© 2025 PatSnap. All rights reserved.Legal|Privacy policy|Modern Slavery Act Transparency Statement|Sitemap|About US| Contact US: help@patsnap.com