Manufacturing method of steam compressor pressure expander
A steam compressor and manufacturing method technology, applied in the field of steam compressors, can solve the problems affecting the diffuser, the deformation of the end face of the diffuser, and the low flatness and verticality of the end face, so as to save milling tooling, ensure the height dimension, The effect of improving the overall quality
- Summary
- Abstract
- Description
- Claims
- Application Information
AI Technical Summary
Problems solved by technology
Method used
Image
Examples
Embodiment Construction
[0039] Embodiments of the present invention will be described in further detail below in conjunction with the accompanying drawings.
[0040] In this embodiment, the orientation or positional relationship indicated by the terms "upper", "lower", "left", "right", "front", "rear", "upper end" and "lower end" are based on the orientation or positional relationship shown in the drawings, It is for the convenience of description only, and does not indicate or imply that the device or element referred to must have a specific orientation, be constructed in a specific orientation, or operate, and thus should not be construed as limiting the present invention.
[0041] During specific implementation: if Figure 1 ~ Figure 4 Shown, a kind of manufacturing method of vapor compressor diffuser comprises the following steps:
[0042] a. Blank heat treatment;
[0043] b. Large end 1, outer circle, inner hole and first step surface 4 of rough-turned diffuser;
[0044] c. Small end 2, outer...
PUM
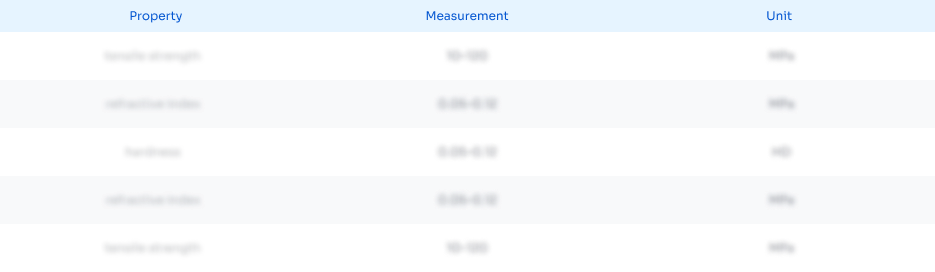
Abstract
Description
Claims
Application Information

- R&D Engineer
- R&D Manager
- IP Professional
- Industry Leading Data Capabilities
- Powerful AI technology
- Patent DNA Extraction
Browse by: Latest US Patents, China's latest patents, Technical Efficacy Thesaurus, Application Domain, Technology Topic, Popular Technical Reports.
© 2024 PatSnap. All rights reserved.Legal|Privacy policy|Modern Slavery Act Transparency Statement|Sitemap|About US| Contact US: help@patsnap.com