Novel structure and machining technique of capillary pipe mesh grating
A capillary and grid technology, which is applied in the field of new capillary grid structure and its processing technology, can solve the problems of delay in construction period, unusable size difference, inability to meet, etc., and achieve the effect of ensuring quality, ensuring smoothness and high product rate.
- Summary
- Abstract
- Description
- Claims
- Application Information
AI Technical Summary
Problems solved by technology
Method used
Image
Examples
Embodiment Construction
[0042] The present invention will be further described in detail below in conjunction with the accompanying drawings, so that those skilled in the art can implement it with reference to the description.
[0043]It should be understood that terms such as "having", "comprising" and "including" as used herein do not entail the presence or addition of one or more other elements or combinations thereof.
[0044] Figure 3-4 A novel capillary grid structure according to the present invention is shown, comprising:
[0045] Multiple capillaries 1;
[0046] Relatively arranged to connect each capillary to form the main pipe 2 of the capillary grid;
[0047] Wherein, each of the dry pipes is respectively provided with a connection part 3 matched with the capillary, and the connection part is further connected with the capillary through the first metal hollow tube 4 to form a capillary grid body. With this scheme, the connecting part with branch structure is set on the prefabricated m...
PUM
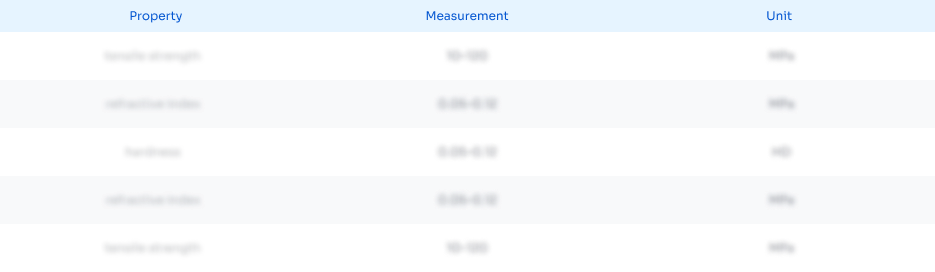
Abstract
Description
Claims
Application Information

- Generate Ideas
- Intellectual Property
- Life Sciences
- Materials
- Tech Scout
- Unparalleled Data Quality
- Higher Quality Content
- 60% Fewer Hallucinations
Browse by: Latest US Patents, China's latest patents, Technical Efficacy Thesaurus, Application Domain, Technology Topic, Popular Technical Reports.
© 2025 PatSnap. All rights reserved.Legal|Privacy policy|Modern Slavery Act Transparency Statement|Sitemap|About US| Contact US: help@patsnap.com