Extra-large drying oven structure provided with carbon fiber barrel
A carbon fiber and oven technology, used in drying, dryers, drying solid materials, etc., can solve the problems of unsafe transportation, heat loss, uneven heating, etc., to improve safety performance, reduce negative effects, and prevent heat loss. Effect
- Summary
- Abstract
- Description
- Claims
- Application Information
AI Technical Summary
Problems solved by technology
Method used
Image
Examples
Embodiment Construction
[0025] The specific content of the present invention will be described in detail below in conjunction with the accompanying drawings and specific embodiments.
[0026] Such as figure 1 , figure 2 , image 3 , Figure 4 , Figure 5 , Image 6 , Figure 7 , Figure 8 , Figure 9 , Figure 10 , Figure 11 , Figure 12 , Figure 13 , Figure 14 , Figure 15As shown, the carbon fiber cylinder super large oven structure includes: a frame 1 and a slide rail 2 arranged in the frame 1, an oven 3 is arranged on the upper end of the frame 1, and a drying chamber is arranged in the oven 3 4. An escalator 5 is provided on the oven 3, and hot air circulation side air ducts 6 are arranged symmetrically on both sides inside the oven 3, and the upper ends of the two hot air circulation side air ducts 6 are arranged on the upper end of the oven 3 The hot air circulation upper air passage 7 communicates with each other, and the hot air circulation air outlet 8 communicating with t...
PUM
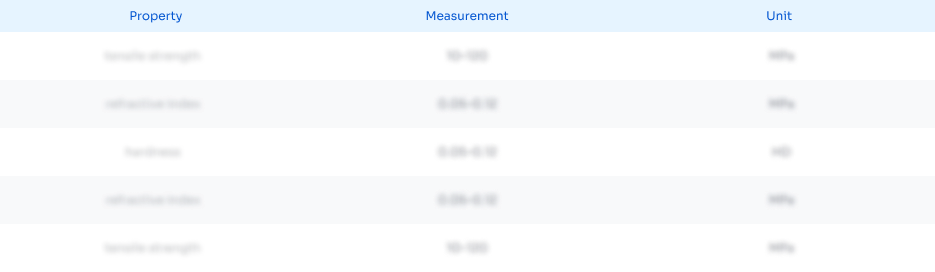
Abstract
Description
Claims
Application Information

- R&D
- Intellectual Property
- Life Sciences
- Materials
- Tech Scout
- Unparalleled Data Quality
- Higher Quality Content
- 60% Fewer Hallucinations
Browse by: Latest US Patents, China's latest patents, Technical Efficacy Thesaurus, Application Domain, Technology Topic, Popular Technical Reports.
© 2025 PatSnap. All rights reserved.Legal|Privacy policy|Modern Slavery Act Transparency Statement|Sitemap|About US| Contact US: help@patsnap.com