Asynchronous motor speed sensorless control method based on improved Q-MRAS
A speed sensorless, asynchronous motor technology, applied in motor generator control, electronic commutation motor control, control system and other directions, can solve the problem of the decline of the estimation effect, achieve strong load capacity, solve the strong dependence of motor parameters, The effect of high speed identification accuracy
- Summary
- Abstract
- Description
- Claims
- Application Information
AI Technical Summary
Problems solved by technology
Method used
Image
Examples
Embodiment Construction
[0026] The present invention will be further described below in conjunction with the description of the drawings and specific embodiments.
[0027] Such as Figure 1 to Figure 14 As shown, an asynchronous motor speed sensorless control method based on the improved Q-MRAS includes the following steps:
[0028] (1) Speed control: According to the deviation between the motor speed estimated by the speed sensorless method and the given speed value, the difference is sent to the speed regulator (PI regulator), and the calculated output is the stator current q-axis The given value of the component;
[0029] (2) Calculation of slip frequency: Calculate the slip angular velocity of the motor according to the q-axis component of the stator current, and add it to the motor speed estimated by the speed sensorless method to obtain the electrical angular velocity of the rotor flux linkage, and pass an integral link The spatial phase of the rotor flux linkage can be obtained;
[0030] ...
PUM
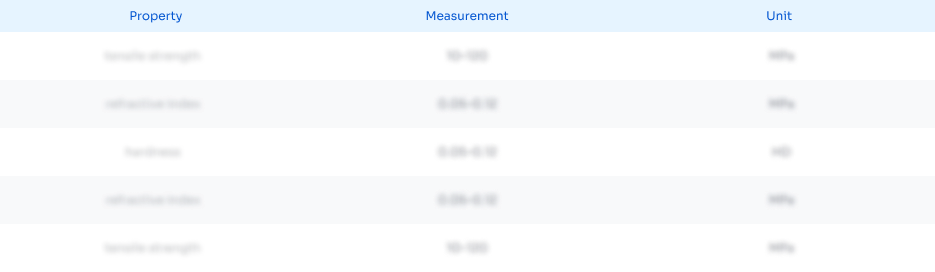
Abstract
Description
Claims
Application Information

- Generate Ideas
- Intellectual Property
- Life Sciences
- Materials
- Tech Scout
- Unparalleled Data Quality
- Higher Quality Content
- 60% Fewer Hallucinations
Browse by: Latest US Patents, China's latest patents, Technical Efficacy Thesaurus, Application Domain, Technology Topic, Popular Technical Reports.
© 2025 PatSnap. All rights reserved.Legal|Privacy policy|Modern Slavery Act Transparency Statement|Sitemap|About US| Contact US: help@patsnap.com