Open type industrial robot controller architecture based on double CPUs and an FPGA
An industrial robot, an open technology, applied in the direction of computer control, program control, general control system, etc., can solve the problems of difficult integration of external hardware, expensive modification of closed systems, etc., to reduce the difficulty of development, realize real-time and synchronization , to achieve the effect of low-level opening
- Summary
- Abstract
- Description
- Claims
- Application Information
AI Technical Summary
Problems solved by technology
Method used
Image
Examples
Embodiment 1
[0020] refer to figure 1 , taking the interface extension as an example to illustrate the openness of the controller. ROS-I extended interface implementation plan: The Controller Layer of ROS-I is the manufacturer's interface layer of the robot controller. Through the interface of this layer and the TCP protocol, the trajectory message can be transmitted from the upper layer ROS-I to the bottom controller. By designing the analysis program, the corresponding position control instructions can be generated, and then the control of the robot can be realized. This part of the interface and functions can be realized by the auxiliary CPU of the controller, providing a hardware controller platform for ROS-I, which can be compared with the main CPU control part, and can also make full use of the research results of ROS-I to improve the controller. performance. Industrial bus expansion interface implementation plan: EtherCAT, POWERLINK, PROFINET and other industrial buses adopt Ether...
Embodiment 2
[0022] refer to figure 2 and image 3, taking performance testing and simulation technology as an example to illustrate the openness of the controller. The implementation plan of the open interface technology of the test system based on the built-in signal: Since the controller adopts a dual-CPU structure, the main control parameters, control variables and system feedback data are shared. The auxiliary CPU can capture all the shared signals inside the robot control system according to the servo control cycle, including: the output of each control loop of the main CPU, feedback information such as motor position, speed, current, and robot end posture information, using synchronous interpolation control signals as signals The collected trigger signal can realize data collection with a maximum collection frequency of 4KHz, and realize real-time communication with a PC through an Ethernet interface. The maximum communication speed is designed to be 1KHz. Acquisition and storage...
PUM
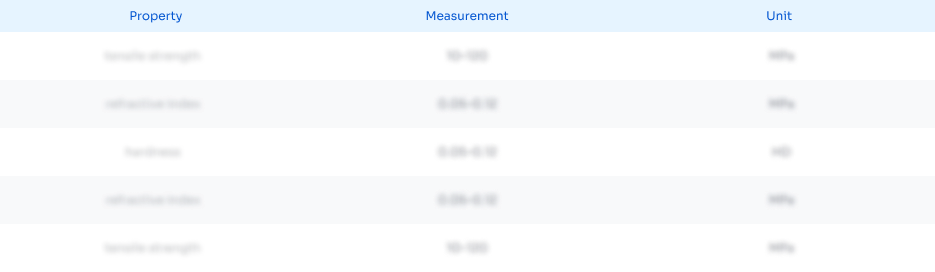
Abstract
Description
Claims
Application Information

- R&D
- Intellectual Property
- Life Sciences
- Materials
- Tech Scout
- Unparalleled Data Quality
- Higher Quality Content
- 60% Fewer Hallucinations
Browse by: Latest US Patents, China's latest patents, Technical Efficacy Thesaurus, Application Domain, Technology Topic, Popular Technical Reports.
© 2025 PatSnap. All rights reserved.Legal|Privacy policy|Modern Slavery Act Transparency Statement|Sitemap|About US| Contact US: help@patsnap.com