A robot machine tool loading workstation system for automobile processing
A technology of working system and workstation, applied in the field of feeding system, can solve the problems of lower production efficiency, health hazards of workers, processing errors, etc., and achieve the effect of ensuring processing quality
- Summary
- Abstract
- Description
- Claims
- Application Information
AI Technical Summary
Problems solved by technology
Method used
Image
Examples
Embodiment 1
[0034] This example figure 1 As shown, a robotic machine tool loading workstation system for automobile processing includes a material carrying system 1, guide rails 2, a robot loading workstation 3, a loading management system 4 and an operator terminal 5,
[0035] The raw material carrying system 1 is used for loading and transporting automobile raw materials, and the raw material carrying system 1 is provided with clamps for clamping automobile raw materials;
[0036] The guide rail 2 is used to lead the raw material carrying system 1 into or out of the robot loading workstation 3;
[0037] The robot feeding workstation 3 is used to place the automobile raw materials to the raw material carrying system 1 docked at the robot feeding workstation 3;
[0038] The loading management system 4 is used to receive and process the status and usage information sent by the current material carrying system 1 and the robot loading workstation 3, direct the operation of the entire loadin...
Embodiment 2
[0042] This embodiment is further improved based on embodiment 1, combining figure 1 and figure 2 As shown, the material carrying system 1 includes a material carrying platform 11, a carrying platform alignment device 12, a carrying platform lock module 13, a carrying platform signal receiving module 14 and a carrying platform signal transmitting module 15,
[0043] The raw material carrying platform 11 is used to carry and clamp the automobile raw materials that need to be processed;
[0044] The carrying platform alignment device 12 is used to align the raw material carrying platform 11 with the robot feeding workstation 3;
[0045] The carrying platform lock module 13 is used to start or stop the movement of the material carrying platform 11;
[0046] The loading platform signal receiving module 14 is used to receive the instruction to unlock the loading platform lock module 13 issued by the loading management system 4 and the movement instruction of the raw material loa...
Embodiment 3
[0050] This embodiment is further improved based on any one of the embodiments 1-2, combined with figure 1 and figure 2 As shown, the robot loading workstation 3 includes a workstation signal receiving module 31, a workstation working system 32 and a workstation signal transmitting module 33,
[0051] The workstation signal receiving module 31 is used to receive the workstation operation instruction issued by the material loading management system 4;
[0052] The workstation working system 32 is used to firmly place the automobile raw materials on the raw material carrying system 1;
[0053] The workstation signal transmitting module 33 is used to send information to the material management system 4 that the work of the workstation working system 32 is completed.
[0054] During use, the workstation signal receiving module 31 receives the workstation operation command issued by the material loading management system 4, and firmly places the automobile raw materials on the m...
PUM
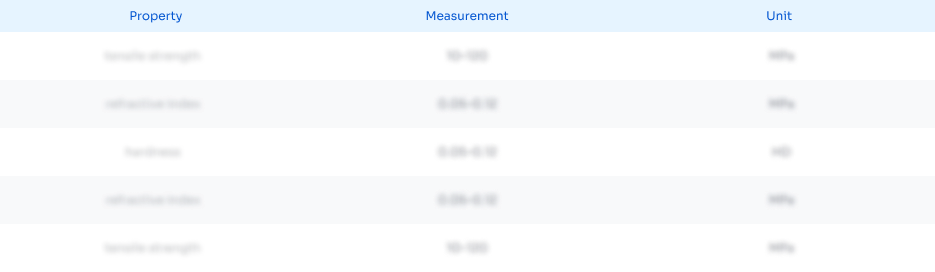
Abstract
Description
Claims
Application Information

- R&D
- Intellectual Property
- Life Sciences
- Materials
- Tech Scout
- Unparalleled Data Quality
- Higher Quality Content
- 60% Fewer Hallucinations
Browse by: Latest US Patents, China's latest patents, Technical Efficacy Thesaurus, Application Domain, Technology Topic, Popular Technical Reports.
© 2025 PatSnap. All rights reserved.Legal|Privacy policy|Modern Slavery Act Transparency Statement|Sitemap|About US| Contact US: help@patsnap.com