Servo wire feeding device for automatic welding robot
An automatic welding and wire feeding device technology, which is applied in welding equipment, welding equipment, auxiliary equipment, etc., can solve the problems of affecting the work of motors and robots, excessive dust, and debris peeled off from welding wire, etc., and achieves compact structure and simple overall structure , Good insulation effect
- Summary
- Abstract
- Description
- Claims
- Application Information
AI Technical Summary
Problems solved by technology
Method used
Image
Examples
Embodiment Construction
[0033] The present invention will be further described below, but the present invention is not limited to the following examples.
[0034] The servo wire feeding method currently uses angle encoder feedback wire feeding and linear sensing wire feeding. The present invention utilizes a linear buffer device to achieve a solution for the synchronization of the wire movement of the welding torch part pushing and pulling mechanism and the wire feeding mechanism.
[0035] Such as Figure 1 to Figure 5 As shown, the servo wire feeding device of the present invention includes a servo wire feeding torch body and a linear buffer of the servo wire feeding device connected to its tail end through a conductive cable.
[0036] The servo wire-feeding welding torch body includes a barrel assembly 34 installed on the front side of the servo wire-feeding welding torch, and an anti-collision sensing device 21. The interior of the servo wire-feeding welding torch body passes through a transition ...
PUM
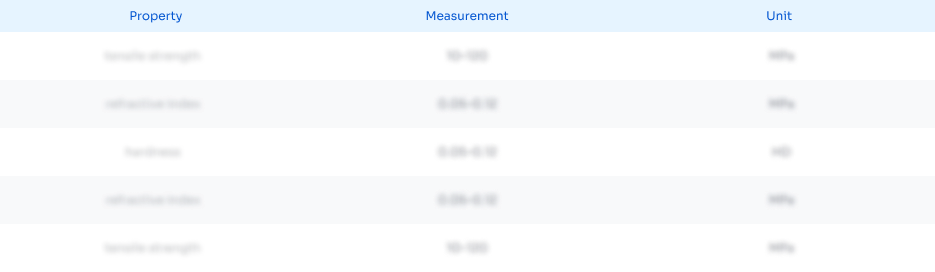
Abstract
Description
Claims
Application Information

- R&D Engineer
- R&D Manager
- IP Professional
- Industry Leading Data Capabilities
- Powerful AI technology
- Patent DNA Extraction
Browse by: Latest US Patents, China's latest patents, Technical Efficacy Thesaurus, Application Domain, Technology Topic, Popular Technical Reports.
© 2024 PatSnap. All rights reserved.Legal|Privacy policy|Modern Slavery Act Transparency Statement|Sitemap|About US| Contact US: help@patsnap.com