A Radial Piezoelectric Actuator Based on Flexible Amplified Structure
A piezoelectric driver, flexible technology, applied in the direction of piezoelectric effect/electrostrictive or magnetostrictive motors, generators/motors, electrical components, etc., can solve the problem of a single output direction of the driver, and improve the radial output Displacement range, simple design and compact structure
- Summary
- Abstract
- Description
- Claims
- Application Information
AI Technical Summary
Problems solved by technology
Method used
Image
Examples
Embodiment 1
[0042] First, the lower end cover 1 is screwed into the bottom of the sleeve 2, and connected through internal and external threads; the small diameter end of the lower end cover 1 is embedded in the inner side of the piezoelectric stack drive unit 4, and the lower surface of the piezoelectric stack drive unit 4 is connected to the inner surface of the piezoelectric stack drive unit 4. The stepped surface of the lower end cover 1 is in contact; the power line of the piezoelectric stack drive unit 4 is led out from the expansion joint 7 on the side wall of the sleeve 2, and the drive power 5 is applied; the small diameter end of the upper end cover 1 is embedded in the piezoelectric stack drive unit 4 Inside, the stepped surface of the upper end cover 1 is in contact with the upper surface of the piezoelectric stack drive unit 4; the large diameter end of the upper end cover 1 has an external thread, and the top of the sleeve 3 has an internal thread, and the end cover 1 is screw...
Embodiment 2
[0044] The difference from Embodiment 1 is that in this embodiment, the end cap 1 and the sleeve 3 do not have external threads and internal threads, and the end cap 1 and the sleeve 2 are fixed by fastening screws 6; the small diameter ends of the upper and lower end caps 1 There is a groove, and the piezoelectric stack driving unit 4 is placed in the groove, and the two ends of the piezoelectric stack driving unit 4 and the end cover are bonded and fixed by epoxy resin.
PUM
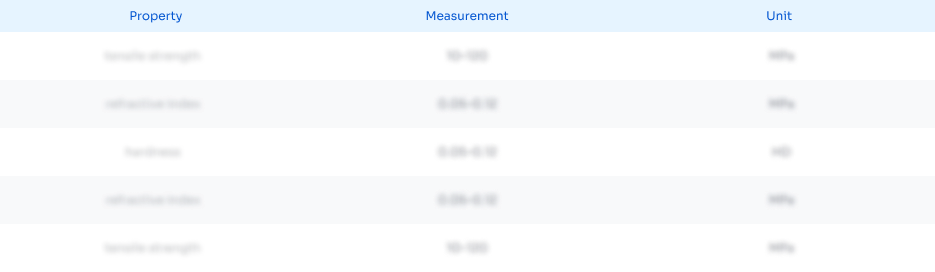
Abstract
Description
Claims
Application Information

- Generate Ideas
- Intellectual Property
- Life Sciences
- Materials
- Tech Scout
- Unparalleled Data Quality
- Higher Quality Content
- 60% Fewer Hallucinations
Browse by: Latest US Patents, China's latest patents, Technical Efficacy Thesaurus, Application Domain, Technology Topic, Popular Technical Reports.
© 2025 PatSnap. All rights reserved.Legal|Privacy policy|Modern Slavery Act Transparency Statement|Sitemap|About US| Contact US: help@patsnap.com