A magnus effect vertical axis wind turbine rotor forward and reverse control and implementation method
An implementation method and technology of wind turbines, applied in the control of wind turbines, wind turbines, engine control, etc., can solve the problems of large mechanical loss, large moment of inertia of cylinders, and difficult commutation
- Summary
- Abstract
- Description
- Claims
- Application Information
AI Technical Summary
Problems solved by technology
Method used
Image
Examples
Embodiment Construction
[0038] In the embodiment of the present invention, a Magnus effect vertical axis wind turbine rotor forward and reverse control and implementation method is provided. According to the on-site wind direction, the orientation of the forward and reverse conversion point of the wind turbine rotor is adjusted in real time, and at the conversion point The dynamic reversing area of the rotor is set before and after the rotor. Through the energy storage mechanism with two buffer wheels with opposite rotation directions, part of the energy of the forward rotation of the rotor can be stored and converted into the starting energy after the rotor reverses. The frequency conversion control motor is fully Using the period of time when the rotor passes through the commutation zone, gradually increase the driving frequency of the motor to a predetermined value based on the starting speed of the rotor inversion and the dynamic characteristics of the system, and reduce the energy consumption in...
PUM
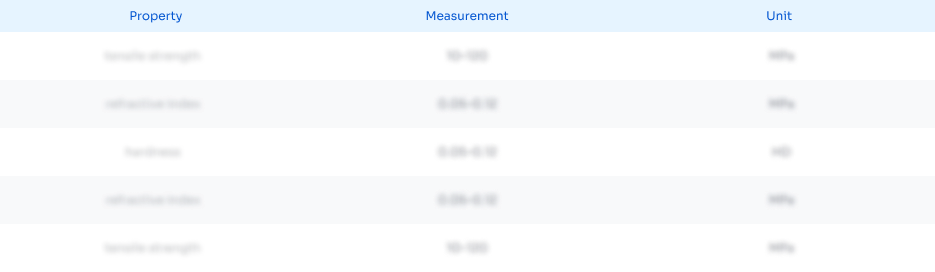
Abstract
Description
Claims
Application Information

- R&D Engineer
- R&D Manager
- IP Professional
- Industry Leading Data Capabilities
- Powerful AI technology
- Patent DNA Extraction
Browse by: Latest US Patents, China's latest patents, Technical Efficacy Thesaurus, Application Domain, Technology Topic, Popular Technical Reports.
© 2024 PatSnap. All rights reserved.Legal|Privacy policy|Modern Slavery Act Transparency Statement|Sitemap|About US| Contact US: help@patsnap.com