Mesoscale turning deformation prediction method
A prediction method and deformation testing technology, applied in special data processing applications, instruments, electrical digital data processing, etc., can solve the problem of unsuitable prediction of mesoscopic scale turning deformation, low accuracy of turning deformation prediction, and mesoscopic scale turning deformation. Inconvenient processing and other problems, to achieve the effect of reducing the number of adjustments, improving processing accuracy, and reducing repeated positioning errors
- Summary
- Abstract
- Description
- Claims
- Application Information
AI Technical Summary
Problems solved by technology
Method used
Image
Examples
Embodiment 1
[0076] ① Determine the calculation model of mesoscopic scale turning cutting force:
[0077] 101 Select the model of the processing machine tool, the number of the turning tool and the material of the workpiece. The workpiece 10 is installed on the fixture, the tool 6 is clamped between the slide table 4 and the pressing plate 5, and is positioned through the stepped surface of the pressing plate. The position of the sliding table is adjusted by the lead screw 9, thereby determining the relative position of the tool tip and the workpiece. Start the machine tool, adjust the cutting depth through the screw 9, and measure the cutting force with a three-way rotating dynamometer. After the measurement signal is collected, use a multi-channel charge amplifier to amplify it, and then obtain the cutting force through data processing.
[0078] The specific parameters of the 102 mesoscale turning experiments are shown in Table 2. The rotational speed, cutting depth and feed rate were s...
PUM
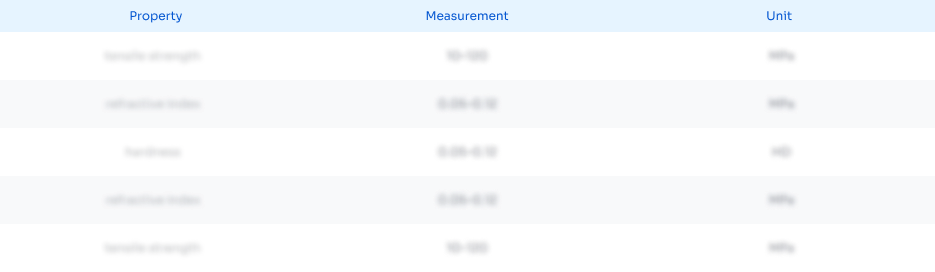
Abstract
Description
Claims
Application Information

- R&D
- Intellectual Property
- Life Sciences
- Materials
- Tech Scout
- Unparalleled Data Quality
- Higher Quality Content
- 60% Fewer Hallucinations
Browse by: Latest US Patents, China's latest patents, Technical Efficacy Thesaurus, Application Domain, Technology Topic, Popular Technical Reports.
© 2025 PatSnap. All rights reserved.Legal|Privacy policy|Modern Slavery Act Transparency Statement|Sitemap|About US| Contact US: help@patsnap.com