Small-size fender simulation device for model test
A simulation device and model test technology, which is applied in the direction of measuring devices, using one-time impact force to test the strength of materials, instruments, etc., can solve the problems of center of gravity position deviation, heavy device weight, floating body moment of inertia change, etc., and achieve the volume of the device and The effects of weight reduction, flexible and convenient use and installation, and simplified structural design
- Summary
- Abstract
- Description
- Claims
- Application Information
AI Technical Summary
Problems solved by technology
Method used
Image
Examples
Embodiment Construction
[0029] In order to understand the above-mentioned purpose, features and advantages of the present invention more clearly, the present invention will be further described below in conjunction with the accompanying drawings and embodiments.
[0030] Specifically, refer to Figure 4 , Figure 5 Explosion diagram of a small fender simulator for model testing, a small fender simulator for model testing, including a base 1, an elastic nesting part connected to the base 1, and a collision head 2 connected to the elastic nesting part; the base 1 and A force sensor 3 is arranged between the elastic nesting parts to measure the force of the simulation device;
[0031] The elastic nesting part includes a through rod 4, an inner sleeve 5, a rear sleeve 6 and a front sleeve 7, and the through rod 4, the rear sleeve 6 and the front sleeve 7 are respectively provided with pressure relief holes S , when used underwater, to drain water from the simulated device; combined with Figure 6 It c...
PUM
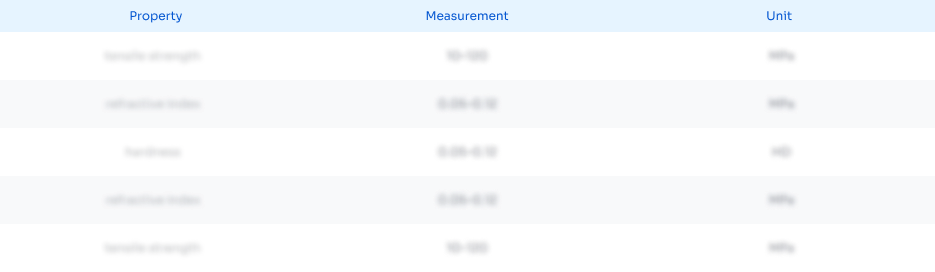
Abstract
Description
Claims
Application Information

- R&D Engineer
- R&D Manager
- IP Professional
- Industry Leading Data Capabilities
- Powerful AI technology
- Patent DNA Extraction
Browse by: Latest US Patents, China's latest patents, Technical Efficacy Thesaurus, Application Domain, Technology Topic, Popular Technical Reports.
© 2024 PatSnap. All rights reserved.Legal|Privacy policy|Modern Slavery Act Transparency Statement|Sitemap|About US| Contact US: help@patsnap.com