Driving shaft bell-shaped housing structure and process treatment method thereof
A processing method and bell-shaped shell technology, applied in heat treatment furnaces, heat treatment equipment, couplings, etc., can solve problems such as performance degradation of mechanical parts, impact on torque performance, and car troubles, achieving high and low temperature impact toughness and ensuring overall hardness Requirements and avoid the effect of impact energy reduction
- Summary
- Abstract
- Description
- Claims
- Application Information
AI Technical Summary
Problems solved by technology
Method used
Image
Examples
Embodiment Construction
[0022] The following are specific embodiments of the present invention and in conjunction with the accompanying drawings, the technical solutions of the present invention are further described, but the present invention is not limited to these embodiments.
[0023] In the figure, the main housing 1; the shaft body 2; the inner space body 3; the upper edge space fitting portion 4; the lower space edge fitting portion 5; the channel 6; the channel chamfering 7; the spline portion 8; the fixed connecting body Part 9; arc surface chamfering section 10; lower concave arc groove 11; fixed slot hole 12; entrance slope 13; lower arc portion 14; lower flaring portion 15; flared portion 18; downwardly inclined connecting portion 19.
[0024] Such as figure 1 As shown, the drive shaft bell-shaped shell structure includes a main housing 1 and a shaft body 2, the main housing 1 and the shaft body 2 are integrally connected, the inner side of the main housing 1 has an inner space body 3, a...
PUM
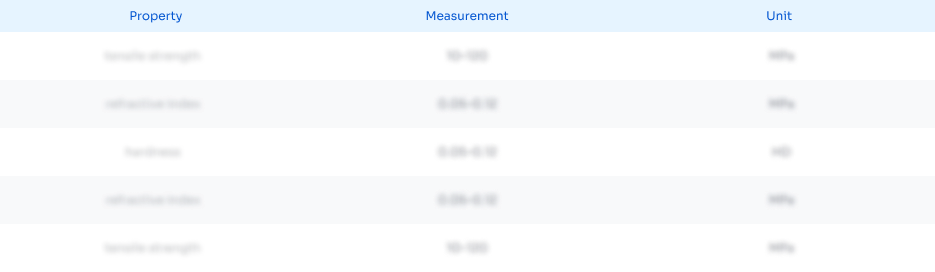
Abstract
Description
Claims
Application Information

- Generate Ideas
- Intellectual Property
- Life Sciences
- Materials
- Tech Scout
- Unparalleled Data Quality
- Higher Quality Content
- 60% Fewer Hallucinations
Browse by: Latest US Patents, China's latest patents, Technical Efficacy Thesaurus, Application Domain, Technology Topic, Popular Technical Reports.
© 2025 PatSnap. All rights reserved.Legal|Privacy policy|Modern Slavery Act Transparency Statement|Sitemap|About US| Contact US: help@patsnap.com