Discharge printing process of reactive dyes based on jet ink printing technology
A reactive dye, discharge printing technology, applied in the direction of dyeing, textile and paper making, etc., can solve the problems of unclear outline of the pattern, inability to perform double-sided discharge, and inability to use inkjet printing, etc., to achieve bright and realistic colors, Small footprint and fast printing
- Summary
- Abstract
- Description
- Claims
- Application Information
AI Technical Summary
Problems solved by technology
Method used
Image
Examples
Embodiment 1
[0026] A reactive dye discharge printing process based on inkjet printing technology includes the following steps: sizing→drying→dying ground color→computer design pattern→preparing discharge ink and spray printing→steaming fixation→washing and drying.
[0027] (1) Sizing treatment: The prescription of the sizing agent is: 30% sodium alginate paste, 3% dispersant, 2% anti-migration agent.
[0028] (2) Drying: Dry the fabric after sizing treatment at 80 to 60% dry.
[0029] (3) Dyeing the ground color: using pad dyeing process for dyeing. The recipe of the reactive dye ground color pad dyeing solution is: reactive dye X: 3%, urea 5%, anti-dyeing salt S 2%, baking soda 2%, sodium alginate paste 50%, total liquid volume 100%.
[0030] (4) Computerized printing and color separation (CAD) editing process: Through the description and editing process, the desired pattern is obtained, and the ink jet nozzle is controlled by the computer.
[0031] (5) Preparation of discharge ink and jet printi...
Embodiment 2
[0045] A reactive dye discharge printing process based on inkjet printing technology includes the following steps: sizing→drying→dying ground color→computer design pattern→preparing discharge ink and spray printing→steaming fixation→washing and drying.
[0046] (1) Sizing treatment: The prescription of the sizing agent is: 35% sodium alginate paste, 4% dispersant, 3% anti-migration agent.
[0047] (2) Drying: Dry the fabric after sizing treatment at 80 to 60% dry.
[0048] (3) Dyeing the ground color: using pad dyeing process for dyeing. The recipe of the reactive dye ground color pad dyeing solution is: reactive dye X: 3%, urea 5%, anti-dyeing salt S 2%, baking soda 2%, sodium alginate paste 60%, total liquid volume 100%.
[0049] (4) Computerized printing and color separation (CAD) editing process: Through the description and editing process, the desired pattern is obtained, and the ink jet nozzle is controlled by the computer.
[0050] (5) Preparation of discharge ink and jet printi...
PUM
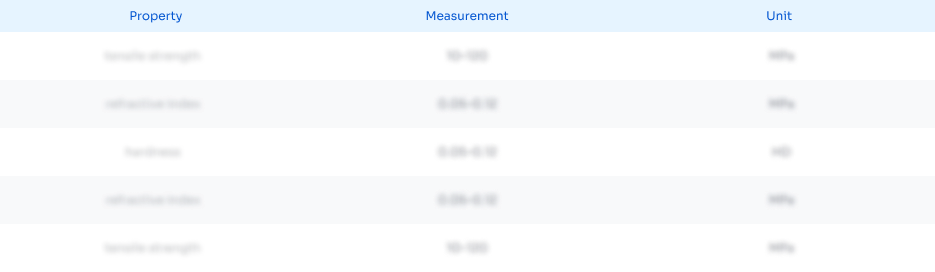
Abstract
Description
Claims
Application Information

- R&D
- Intellectual Property
- Life Sciences
- Materials
- Tech Scout
- Unparalleled Data Quality
- Higher Quality Content
- 60% Fewer Hallucinations
Browse by: Latest US Patents, China's latest patents, Technical Efficacy Thesaurus, Application Domain, Technology Topic, Popular Technical Reports.
© 2025 PatSnap. All rights reserved.Legal|Privacy policy|Modern Slavery Act Transparency Statement|Sitemap|About US| Contact US: help@patsnap.com