Array type parallel laser projection three-dimensional scanning method
A technology of laser projection and three-dimensional scanning, applied in the direction of using optical devices, measuring devices, instruments, etc., can solve the problems of discrete projection pixels, affecting the accuracy of three-dimensional scanning, nonlinearity of light intensity, etc.
- Summary
- Abstract
- Description
- Claims
- Application Information
AI Technical Summary
Problems solved by technology
Method used
Image
Examples
Embodiment Construction
[0024] The present invention will be described in detail below in conjunction with the accompanying drawings.
[0025] An array parallel laser projection three-dimensional scanning device ( Figure 1 As shown), it includes a laser micro-mirror projection device for projecting laser light in different directions and two or more array cameras for data acquisition, and the cameras are distributed in an array around the laser projection device.
[0026] An arrayed parallel laser projection three-dimensional scanning system specifically includes the following steps:
[0027] The first step is to calibrate the system parameters.
[0028] Before scanning the measured object, calibrate the internal parameters of the camera and the pose relationship between the camera and the laser plane. In this step, a group of monocular systems and a group of binocular systems are taken as examples to introduce the specific calibration process.
[0029] (1) Calibrate the internal and external par...
PUM
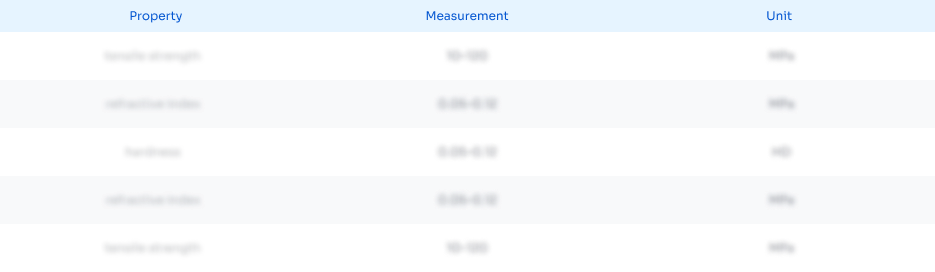
Abstract
Description
Claims
Application Information

- Generate Ideas
- Intellectual Property
- Life Sciences
- Materials
- Tech Scout
- Unparalleled Data Quality
- Higher Quality Content
- 60% Fewer Hallucinations
Browse by: Latest US Patents, China's latest patents, Technical Efficacy Thesaurus, Application Domain, Technology Topic, Popular Technical Reports.
© 2025 PatSnap. All rights reserved.Legal|Privacy policy|Modern Slavery Act Transparency Statement|Sitemap|About US| Contact US: help@patsnap.com