Method of preparing artificial rutile with ferric salt solution leaching method
A technology of artificial rutile and leaching method, applied in the field of chemical metallurgy, can solve the problems of complex process and equipment, too long reaction time, etc., and achieve the effects of reducing equipment investment and operating costs, reducing energy consumption, and reducing emissions
- Summary
- Abstract
- Description
- Claims
- Application Information
AI Technical Summary
Benefits of technology
Problems solved by technology
Method used
Image
Examples
Embodiment 1
[0036] The processing steps of the method for preparing artificial rutile by the iron salt solution leaching method of the present embodiment are:
[0037] (1) After mixing titanium concentrate and reduced coal at a mass ratio of 3:1, put it into the kiln for calcination from the kiln tail of the rotary kiln, and at the same time blow natural gas into the kiln head with a spray gun. The calcination temperature is 1120°C and the calcination time is 12h , the material after calcination enters the cooling kiln, and the temperature of the material after cooling is 45 ° C. After leaving the kiln, it is screened and magnetically separated to obtain ferro-titanium fine powder with a metallization rate of 90.8%;
[0038] (2) the ferro-titanium fine powder obtained by step (1) is continuously added in the net solution of iron salt, and leaching reaction is carried out, and the elemental iron in the ferro-titanium fine powder is reduced to ferrous iron salt by the ferric salt; the leachi...
Embodiment 2
[0044] The processing steps of the method for preparing artificial rutile by the iron salt solution leaching method of the present embodiment are:
[0045] (1) After mixing titanium concentrate and reduced coal at a mass ratio of 4:1, press it into pellets with a diameter of 40mm through a high-pressure roller press, and put them into a rotary hearth furnace for calcination. The calcination temperature is 1350°C, and the calcination time is 0.5h. After calcination, the material enters the cooling cylinder. After cooling, the temperature of the pellets is 50°C. After the pellets are crushed, sieved, and magnetically separated, ferro-titanium powder with a metallization rate of 92.1% is obtained;
[0046] (2) Add 92% concentrated sulfuric acid to the reaction pot, then add iron fine powder, stir, the mass ratio of concentrated sulfuric acid to iron fine powder is 1.40:1; then add water to the reaction pot while stirring to trigger acidolysis Reaction, after the mixture has acido...
Embodiment 3
[0053] The processing steps of the method for preparing artificial rutile by the iron salt solution leaching method of the present embodiment are:
[0054] (1) After mixing titanium concentrate and reduced coal at a mass ratio of 5:1, the kiln head of the tunnel kiln is put into the kiln for calcination. The temperature of the calcination kiln is 1180°C, and the calcination time is 16 hours. The temperature of the material after coming out of the tunnel kiln is At 55°C, after leaving the kiln, the material is crushed, screened, and magnetically separated to obtain ferro-titanium fine powder with a metallization rate of 89.7%;
[0055] (2) 93% concentrated sulfuric acid is added in the reaction pot, then add ilmenite concentrate, stir, the mass ratio of concentrated sulfuric acid and iron concentrate powder is 1.60:1; Stir while adding water in the reaction pot to cause acidolysis reaction, After the acidolysis reaction of the mixture, the reaction acid concentration is control...
PUM
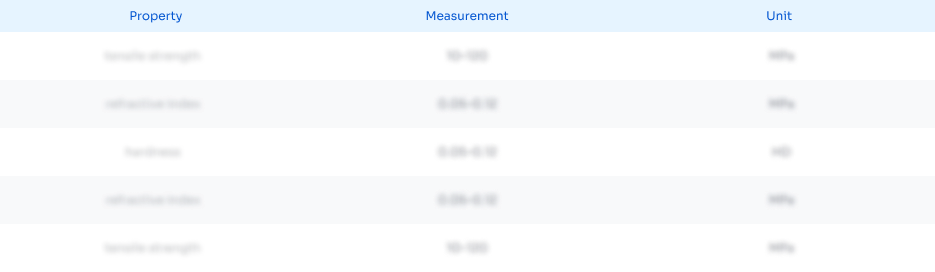
Abstract
Description
Claims
Application Information

- R&D
- Intellectual Property
- Life Sciences
- Materials
- Tech Scout
- Unparalleled Data Quality
- Higher Quality Content
- 60% Fewer Hallucinations
Browse by: Latest US Patents, China's latest patents, Technical Efficacy Thesaurus, Application Domain, Technology Topic, Popular Technical Reports.
© 2025 PatSnap. All rights reserved.Legal|Privacy policy|Modern Slavery Act Transparency Statement|Sitemap|About US| Contact US: help@patsnap.com