Finishing process for glued interweaved fabric
A technology of fabric and viscose, which is applied in the processing of textile materials, liquid/gas/steam open-width fabric processing, fiber processing, etc., and can solve problems such as inability to shape or stretch, cannot be restored, and large differences in moisture content.
- Summary
- Abstract
- Description
- Claims
- Application Information
AI Technical Summary
Problems solved by technology
Method used
Examples
Embodiment 1
[0030] The fabric specification of this craft is DTY75D×R120D 173×120
[0031] 1) Put dry cloth on the machine, add 800L of water, run 4 times at 16°C, and drain;
[0032] 2) The refining and dyeing process is omitted;
[0033] 3) Roll down the dyed wet cloth onto the A-frame, and keep the wet cloth roll at a constant speed of 20 r / min;
[0034] 4) Multi-drum dryer absorbs water (control the moisture content of the fabric at 58%)--padding and softening finishing solution (control the moisture content of the fabric at 67%)+drying (drying temperature 130°C, drying process adopts Dried by a multi-drum finishing machine, the moisture content of the cloth surface is 13% when the cloth is dropped after drying; the composition of the softening finishing liquid includes: polyether polyester chain block silicone oil 15 g / L, epoxy polyether silicone oil 5 g / L L, crosslinking agent 600 2.0 g / L, glacial acetic acid 0.45g / L;
[0035] 5) Stenter at 160°C, spray steam to give 5% humidity,...
Embodiment 2
[0037] The fabric specification of this craft is DTY75D×R120D 173×120
[0038] 1) After stentering, the gray cloth is wetted by 60% by a humidifier, and then unrolled into a chartered car for full "wet pretreatment";
[0039] 2) Apply wet cloth to the machine, add 500L of water, run 2 times at 16°C, and drain;
[0040] 3) The refining and dyeing process is omitted;
[0041] 4) Roll down the dyed wet cloth to the A-frame, and keep the wet cloth roll at a constant speed of 19 r / min:;
[0042] 5) Multi-drum dryer absorbs water (control the moisture content of the fabric at 58%)--padding and softening finishing solution (control the moisture content of the fabric at 67%)+drying (drying temperature 130°C, drying process adopts Dried by a multi-drum finishing machine, the moisture content of the cloth surface is 14% when the cloth is dropped after drying;
[0043]The composition of the softening finishing liquid includes: polyether polyester chain block silicone oil 15g / L, epoxy ...
Embodiment 3
[0046] The fabric specification of this craft is DTY75D×R120D 173×120
[0047] 1) After stentering, the gray cloth is wetted by 60% by a humidifier, and then unrolled into a chartered car for full "wet pretreatment";
[0048] 2) Apply wet cloth to the machine, add 500L of water, run 2 times at 17°C, and drain;
[0049] 3) The refining and dyeing process is omitted;
[0050] 4) Roll down the dyed wet cloth to the A-frame, and keep the wet cloth roll at a constant speed of 21 r / min:;
[0051] 5) Multi-drum dryer absorbs water (control the moisture content of the fabric at 57%)--padding and softening finishing solution (control the moisture content of the fabric at 68%) + drying (the drying temperature is 130°C, and the drying process adopts Dried by a multi-drum finishing machine, the moisture content of the cloth surface is 12% when the cloth is dropped after drying;
[0052] The composition of the softening finishing liquid includes: polyether polyester chain block silicone...
PUM
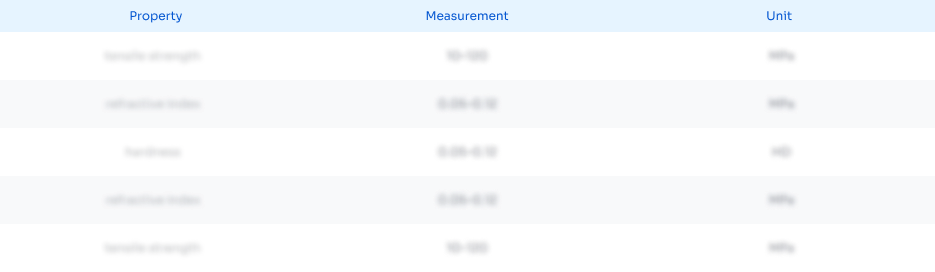
Abstract
Description
Claims
Application Information

- Generate Ideas
- Intellectual Property
- Life Sciences
- Materials
- Tech Scout
- Unparalleled Data Quality
- Higher Quality Content
- 60% Fewer Hallucinations
Browse by: Latest US Patents, China's latest patents, Technical Efficacy Thesaurus, Application Domain, Technology Topic, Popular Technical Reports.
© 2025 PatSnap. All rights reserved.Legal|Privacy policy|Modern Slavery Act Transparency Statement|Sitemap|About US| Contact US: help@patsnap.com