Ultrahigh-pressure sensor of stress attenuation structure
A technology of ultra-high pressure and stress attenuation, which is applied in the direction of fluid pressure measurement, instrumentation, and measurement force by changing the ohmic resistance, which can solve the problems of increasing the pressure measurement range, small pressure loading area, plastic deformation, etc., and increase the upper limit of measurement Effect
- Summary
- Abstract
- Description
- Claims
- Application Information
AI Technical Summary
Problems solved by technology
Method used
Image
Examples
Embodiment Construction
[0016] The present invention will be described in more detail below in conjunction with the accompanying drawings.
[0017] refer to figure 1 , figure 2 , an ultrahigh pressure sensor with a stress attenuation structure, an ultrahigh pressure sensor with a stress attenuation structure, comprising a base 1, an upper cover 3 and a metal pressure bearing element 4, the bottom of the metal pressure bearing element 4 is installed on the base 1, An upper cover 3 is installed on the outside of the metal pressure-bearing element 4, and the base 1 and the upper cover 3 are fastened and connected by four uniformly distributed bolts 8. The top of the upper cover 3 is connected with a pressure-inducing element 5, and the metal pressure-bearing element 4 The upper part is a cone with a gradually larger cross-section. The external pressure directly acts on the smallest pressure surface at the top of the cone. When the pressure propagates in the variable cross-section area, it will gradual...
PUM
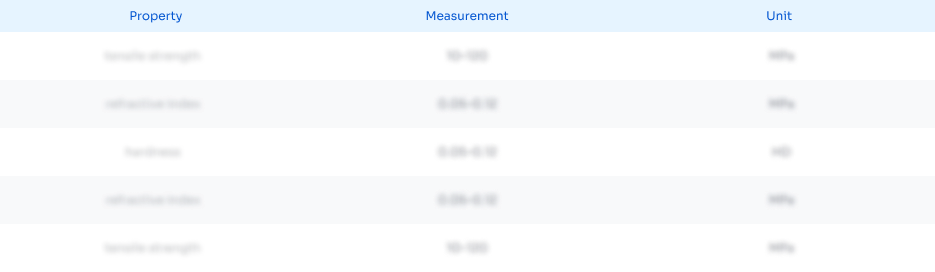
Abstract
Description
Claims
Application Information

- R&D Engineer
- R&D Manager
- IP Professional
- Industry Leading Data Capabilities
- Powerful AI technology
- Patent DNA Extraction
Browse by: Latest US Patents, China's latest patents, Technical Efficacy Thesaurus, Application Domain, Technology Topic, Popular Technical Reports.
© 2024 PatSnap. All rights reserved.Legal|Privacy policy|Modern Slavery Act Transparency Statement|Sitemap|About US| Contact US: help@patsnap.com