Modified ABS (Acrylonitrile Butadiene Styrene) bamboo consumable for 3D printing
A 3D printing and consumable technology, applied in the field of 3D printing consumables, can solve the problems of poor thermal stability, high brittleness, pungent smell, etc., and achieve the effect of reducing the cost of consumables, improving performance, and not easy to warp
- Summary
- Abstract
- Description
- Claims
- Application Information
AI Technical Summary
Problems solved by technology
Method used
Image
Examples
Embodiment Construction
[0017] The present invention is further described by the following examples.
[0018] The invention provides a modified ABS bamboo consumable for 3D printing, which is specifically realized through the following technical scheme: the formula of ABS-based modified bamboo 3D printing consumable is as follows, bamboo fiber 10%-22%, ABS plastic 60%- 77%, coupling agent 1%-2%, hollow microsphere 0.5%-1%, lubricant 0.5%-1%, antioxidant 1%-2%, toughening agent 2%-2.5%, plasticizer 5 %-9.3%, compatibilizer 1%-2%. After the above raw materials are blended, they are granulated by a twin-screw extruder, and the granules are made into filaments with a diameter of 1.75±0.05mm by a 3D printing consumable extruder.
[0019] In each link, the specific parameters are as follows:
[0020] Bamboo fiber is bamboo fiber made from natural clustered bamboo. The purity of the above-mentioned ABS plastic is above 99%, and it is used after being dried.
[0021] The coupling agent is one or more of s...
PUM
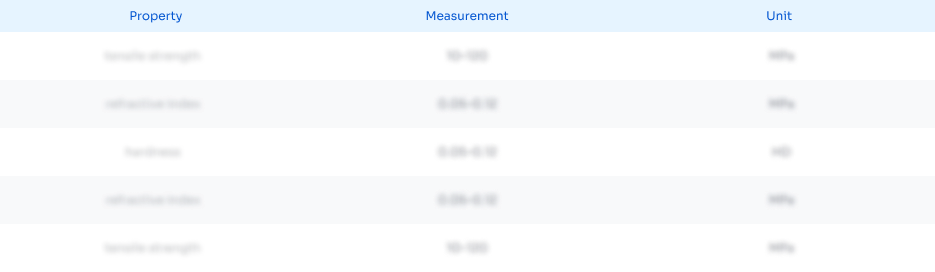
Abstract
Description
Claims
Application Information

- R&D Engineer
- R&D Manager
- IP Professional
- Industry Leading Data Capabilities
- Powerful AI technology
- Patent DNA Extraction
Browse by: Latest US Patents, China's latest patents, Technical Efficacy Thesaurus, Application Domain, Technology Topic, Popular Technical Reports.
© 2024 PatSnap. All rights reserved.Legal|Privacy policy|Modern Slavery Act Transparency Statement|Sitemap|About US| Contact US: help@patsnap.com