Returned sand treatment device and method for sand mould 3D printing
A 3D printing and processing device technology, applied in the field of 3D printing, can solve the problems of exacerbating printing operation costs, environmental pollution, waste of resources, etc., and achieve the effects of saving materials, reducing costs, and avoiding pollution
- Summary
- Abstract
- Description
- Claims
- Application Information
AI Technical Summary
Problems solved by technology
Method used
Image
Examples
Embodiment 1
[0030] Please refer to figure 2 , this embodiment provides a device for processing old sand for sand mold 3D printing.
[0031] The device includes a feeding device, a roasting furnace 6, a conveying device and a collecting device.
[0032] The feeding device is an old sand hopper 1 for containing used sand, and a valve 2 is provided at the lower end of the old sand hopper 1 for controlling the feeding of the old sand in the old sand hopper 1 .
[0033] A sand level meter 3 is arranged at the lower end of the valve 2, and when the sand level meter 3 detects that there is no sand in the old sand bucket 1, the operation of the whole device will be stopped.
[0034] The lower end of the sand level meter 3 is provided with a lower sand pipe 4, so that the feeding device is connected with the roasting furnace 6. The middle part of the lower sand pipe 4 is provided with a horizontally arranged bypass pipeline, which is an exhaust pipe 5, which is used to discharge the gas generat...
Embodiment 2
[0041] Please refer to figure 1 , this embodiment provides a method for processing old sand from sand mold 3D printing, using the device in Embodiment 1 for processing.
[0042] Concentrate the recovered old sand in the old sand bucket. When a certain amount of sand is reached, open the valve at the lower end to fill the roasting furnace by the flow of sand by its own weight. The sand dunes formed by the self-accumulation of sand will leave space in the roasting furnace, which is convenient for the subsequent roasting process. in the exhaust.
[0043] Turn on the power, heat the old sand in the roasting furnace through the heating tube, and at the same time, the temperature measuring couple in the roasting furnace will detect the temperature of the old sand. When the preset roasting temperature of 350°C is reached, the heat preservation timer will start.
[0044] Heat preservation for 80 minutes. After the heat preservation time is up, the signal starts the motor of the screw...
Embodiment 3
[0048] Please refer to figure 1 , this embodiment provides a method for processing old sand from sand mold 3D printing, using the device in Embodiment 1 for processing.
[0049] The method adopted in this example is basically the same as that in Example 2, the difference is that the preset calcination temperature in this example is 450° C., and the holding time is 60 minutes.
PUM
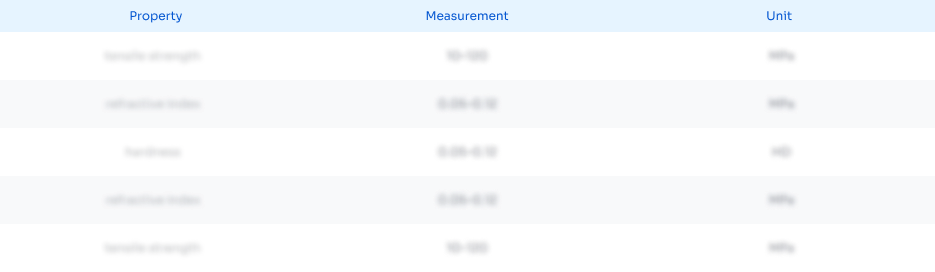
Abstract
Description
Claims
Application Information

- R&D Engineer
- R&D Manager
- IP Professional
- Industry Leading Data Capabilities
- Powerful AI technology
- Patent DNA Extraction
Browse by: Latest US Patents, China's latest patents, Technical Efficacy Thesaurus, Application Domain, Technology Topic, Popular Technical Reports.
© 2024 PatSnap. All rights reserved.Legal|Privacy policy|Modern Slavery Act Transparency Statement|Sitemap|About US| Contact US: help@patsnap.com