A method for synchronous recovery of mercury in spent mercury catalysts and regenerated activated carbon
A waste mercury catalyst and activated carbon technology, applied in chemical instruments and methods, separation methods, chemical recovery, etc., can solve the problems of complicated process, low recovery rate of mercury chloride and activated carbon regeneration, and achieve high recovery rate of mercury and significant economic value , The process is clean and pollution-free
- Summary
- Abstract
- Description
- Claims
- Application Information
AI Technical Summary
Problems solved by technology
Method used
Image
Examples
Embodiment 1
[0020] Embodiment 1: as figure 1 Shown, a method for synchronously reclaiming mercury in waste mercury catalysts and regenerating activated carbon, the specific steps are as follows:
[0021] (1) Mix 100g of waste mercury catalyst and lye (the concentration of lye is 0.1mol / L, and the lye is a mixed solution of sodium hydroxide and calcium hydroxide) and soak them under ultrasonic conditions at a temperature of 90°C 1h obtains mixture A, wherein the solid-to-liquid ratio g:mL of waste mercury catalyst and lye is 1:1, the ultrasonic frequency is 2500 Hz, and the ultrasonic power is 10W;
[0022] (2) Filter the mixture A obtained in step (1) to obtain the filtrate and filter residue, and return the filtrate to step (1) to replace the lye for soaking;
[0023] (3) Under the condition of activated gas (activated gas is carbon dioxide gas), microwave the filter residue obtained in step (2) for 50 minutes to obtain regenerated activated carbon and tail gas I, wherein the power of m...
Embodiment 2
[0026] Embodiment 2: as figure 1 Shown, a method for synchronously reclaiming mercury in waste mercury catalysts and regenerating activated carbon, the specific steps are as follows:
[0027] (1) Mix 100g of waste mercury catalyst and lye (the concentration of lye is 10mol / L, and the lye is a mixed solution of sodium hydroxide and ammonia water) and soak for 3 hours under ultrasonic conditions at a temperature of 60°C to obtain a mixture A, wherein the solid-to-liquid ratio g:mL of waste mercury catalyst and lye is 1:4, the ultrasonic frequency is 1500 Hz, and the ultrasonic power is 100W;
[0028] (2) Filter the mixture A obtained in step (1) to obtain the filtrate and filter residue, and return the filtrate to step (1) to replace the lye for soaking;
[0029] (3) Under the condition of activated gas (the activated gas is carbon dioxide gas), microwave the filter residue obtained in step (2) for 10 minutes to obtain regenerated activated carbon and tail gas I, wherein the po...
Embodiment 3
[0032] Embodiment 3: as figure 1 Shown, a method for synchronously reclaiming mercury in waste mercury catalysts and regenerating activated carbon, the specific steps are as follows:
[0033] (1) Soak 100g of waste mercury catalyst and lye (the concentration of lye is 20mol / L, and the lye is sodium hydroxide solution) for 4 hours under ultrasonic conditions at a temperature of 70°C to obtain mixture A, in which the waste mercury catalyst The solid-to-liquid ratio g:mL of lye is 1:6, the ultrasonic frequency is 20Hz, and the ultrasonic power is 200W;
[0034] (2) Filter the mixture A obtained in step (1) to obtain the filtrate and filter residue, and return the filtrate to step (1) to replace the lye for soaking;
[0035] (3) Under the condition of activated gas (the activated gas is water vapor), microwave the filter residue obtained in step (2) for 180 minutes to obtain regenerated activated carbon and tail gas I, wherein the power of microwave roasting is 50W;
[0036] (4)...
PUM
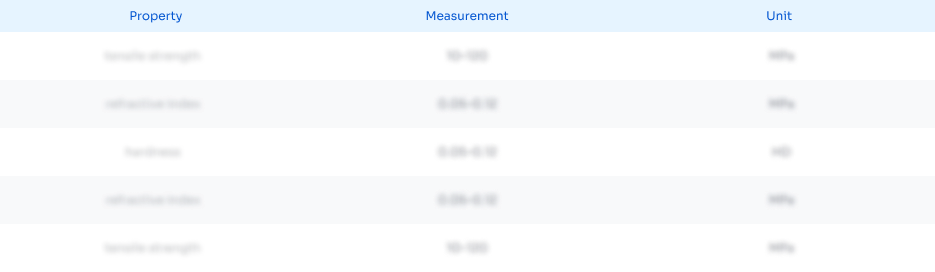
Abstract
Description
Claims
Application Information

- Generate Ideas
- Intellectual Property
- Life Sciences
- Materials
- Tech Scout
- Unparalleled Data Quality
- Higher Quality Content
- 60% Fewer Hallucinations
Browse by: Latest US Patents, China's latest patents, Technical Efficacy Thesaurus, Application Domain, Technology Topic, Popular Technical Reports.
© 2025 PatSnap. All rights reserved.Legal|Privacy policy|Modern Slavery Act Transparency Statement|Sitemap|About US| Contact US: help@patsnap.com