Nickel plating method for electroplating bright nickel silver
A nickel-silver, nickel-plating technology, applied in the field of surface treatment, can solve the problems of poor wear resistance, low hardness, discoloration, etc., and achieve the effect of improving light reflectivity, good wear resistance, and high uniformity
- Summary
- Abstract
- Description
- Claims
- Application Information
AI Technical Summary
Problems solved by technology
Method used
Examples
Embodiment 1
[0026] A nickel plating method for electroplating bright nickel silver, comprising the steps of:
[0027] (1) Polishing: polishing the surface of the raw material;
[0028] (2) Degreasing: that is, the surface of the raw material is degreased by a degreasing agent;
[0029] (3) Micro-etching: that is, micro-etching the raw materials through micro-etching liquid;
[0030] (4) electroplating bright nickel: be about to place raw material in the electroplating bright nickel liquid that pH value is 3 and apply plating;
[0031] (5) Sulfuric acid washing: promptly use the sulfuric acid of concentration 3% to clean the raw material after plating;
[0032] (6) Pre-silvering: put the cleaned raw materials in the pre-silvering solution for pre-silvering;
[0033] (7) Silver plating: put the pre-silvered raw material in the silver plating solution for silver plating again;
[0034] (8) Washing: the raw material after silver plating is cleaned with clear water;
[0035] (9) drying. ...
Embodiment 2
[0043] A nickel plating method for electroplating bright nickel silver, comprising the steps of:
[0044] (1) Polishing: polishing the surface of the raw material;
[0045] (2) Degreasing: that is, the surface of the raw material is degreased by a degreasing agent;
[0046] (3) Micro-etching: that is, micro-etching the raw materials through micro-etching liquid;
[0047] (4) electroplating bright nickel: be about to place raw material in the electroplating bright nickel liquid that pH value is 4 and apply plating;
[0048] (5) Sulfuric acid washing: promptly use the sulfuric acid of concentration 4% to clean the raw material after plating;
[0049] (6) Pre-silvering: put the cleaned raw materials in the pre-silvering solution for pre-silvering;
[0050] (7) Silver plating: put the pre-silvered raw material in the silver plating solution for silver plating again;
[0051] (8) Washing: the raw material after silver plating is cleaned with clear water;
[0052] (9) drying. ...
Embodiment 3
[0060] A nickel plating method for electroplating bright nickel silver, comprising the steps of:
[0061] (1) Polishing: polishing the surface of the raw material;
[0062] (2) Degreasing: that is, the surface of the raw material is degreased by a degreasing agent;
[0063] (3) Micro-etching: that is, micro-etching the raw materials through micro-etching liquid;
[0064] (4) electroplating bright nickel: be about to place raw material in the electroplating bright nickel liquid that pH value is 5 and apply plating;
[0065] (5) Sulfuric acid washing: promptly use the sulfuric acid of concentration 5% to clean the raw material after plating;
[0066] (6) Pre-silvering: put the cleaned raw materials in the pre-silvering solution for pre-silvering;
[0067] (7) Silver plating: put the pre-silvered raw material in the silver plating solution for silver plating again;
[0068] (8) Washing: the raw material after silver plating is cleaned with clear water;
[0069] (9) drying. ...
PUM
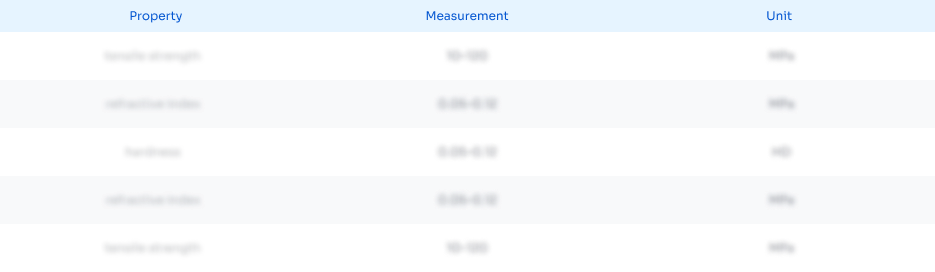
Abstract
Description
Claims
Application Information

- Generate Ideas
- Intellectual Property
- Life Sciences
- Materials
- Tech Scout
- Unparalleled Data Quality
- Higher Quality Content
- 60% Fewer Hallucinations
Browse by: Latest US Patents, China's latest patents, Technical Efficacy Thesaurus, Application Domain, Technology Topic, Popular Technical Reports.
© 2025 PatSnap. All rights reserved.Legal|Privacy policy|Modern Slavery Act Transparency Statement|Sitemap|About US| Contact US: help@patsnap.com