Production process for ultrapure iron concentrate powder
A production process, ultra-pure iron technology, applied in the field of mineral processing, can solve the problems of large environmental impact and high production cost, and achieve the effect of low equipment cost, low cost and high grade
- Summary
- Abstract
- Description
- Claims
- Application Information
AI Technical Summary
Problems solved by technology
Method used
Image
Examples
Embodiment 1
[0020] Embodiment 1: The production process of the ultra-pure iron fine powder adopts the following specific processes.
[0021] (1) The concentrate slurry with a grade of 67.3wt% is screened through a -200 mesh high-frequency fine sieve, and the product under the screen is subjected to magnetic separation twice by a magnetic separator with a magnetic field strength of 1000Gs, and the obtained magnetic concentrate grade is 71.4 wt%;
[0022] (2) The above-mentioned magnetic separation concentrate was elutriated twice, and the magnetic field strength was 7KA / m; the obtained ultra-concentrate grade was 72.02wt%, and the Si content was 0.4wt%;
[0023] (3) The ultra-pure ore is dehydrated and dried to obtain ultra-pure iron concentrate; the yield of ultra-pure iron concentrate is 79.6%, and the obtained comprehensive tailings grade is 58.7wt%.
Embodiment 2
[0024] Embodiment 2: The production process of the ultra-pure iron fine powder adopts the following specific process.
[0025] (1) The concentrate slurry with a grade of 67.8wt% is screened through a -200 mesh high-frequency fine sieve, and the products under the screen are subjected to magnetic separation for 3 times by a magnetic separator with a magnetic field strength of 1000Gs, and the obtained magnetic concentrate grade is 71.8 wt%;
[0026] (2) The above-mentioned magnetic separation concentrate was elutriated twice, and the magnetic field strength was 7KA / m; the obtained ultra-concentrate grade was 72.09wt%, and the Si content was 0.31wt%;
[0027] (3) The ultra-pure ore is dehydrated and dried to obtain ultra-pure iron concentrate; the yield of ultra-pure iron concentrate is 79.4%, and the obtained comprehensive tailings grade is 59.6wt%.
Embodiment 3
[0028] Embodiment 3: The production process of the ultra-pure iron fine powder adopts the following specific process.
[0029] (1) The concentrate pulp with a grade of 67.1wt% is screened through a -200 mesh high-frequency fine sieve, and the product under the screen is subjected to magnetic separation twice by a magnetic separator with a magnetic field strength of 1100Gs, and the obtained magnetic concentrate grade is 71.4 wt%;
[0030] (2) The above-mentioned magnetic separation concentrate was elutriated three times, and the magnetic field strength was 6KA / m; the obtained ultra-concentrate grade was 72.1wt%, and the Si content was 0.3wt%;
[0031] (3) The ultra-pure iron concentrate can be obtained by dehydrating and drying the ultra-concentrate; the yield of the ultra-pure iron concentrate is 79.5%, and the obtained comprehensive tailings grade is 58.7wt%.
PUM
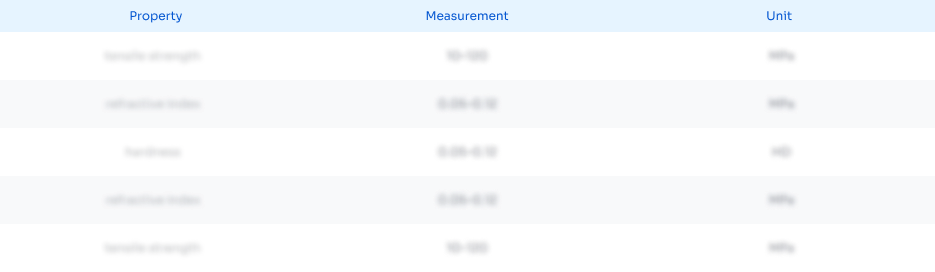
Abstract
Description
Claims
Application Information

- Generate Ideas
- Intellectual Property
- Life Sciences
- Materials
- Tech Scout
- Unparalleled Data Quality
- Higher Quality Content
- 60% Fewer Hallucinations
Browse by: Latest US Patents, China's latest patents, Technical Efficacy Thesaurus, Application Domain, Technology Topic, Popular Technical Reports.
© 2025 PatSnap. All rights reserved.Legal|Privacy policy|Modern Slavery Act Transparency Statement|Sitemap|About US| Contact US: help@patsnap.com