Partition local fairing weight factor-based T-spline curved-surface fitting method
A spline surface and fairing weight technology, applied in image data processing, 3D modeling, instruments, etc., can solve problems such as low precision, difficulty in satisfying different areas at the same time, affecting calculation efficiency, etc., and achieve the effect of improving quality
- Summary
- Abstract
- Description
- Claims
- Application Information
AI Technical Summary
Problems solved by technology
Method used
Image
Examples
specific Embodiment approach
[0080] Construct the fitting equation of each triangular mesh vertex, construct the smoothness equation of each smoothness inspection point according to the local smoothness weight and the global smoothness weight of each smoothness inspection point, and form a hyperparameter about the control point coordinates Determining the system of equations, using the least squares method to solve the overdetermined system of equations about the coordinates of the control points, to obtain the fitting coordinates of the surface control points, the specific implementation is as follows:
[0081] For the tth triangular mesh vertex, its coordinates are marked as Q t =[x t ,y t ,z t ], the coordinates of the parameter field are marked as [u t ,v t ], the fitting equation can be constructed:
[0082]
[0083] where P k is the Euclidean space coordinate of the kth control point, R k (u,v) is the rational mixed basis function corresponding to the control point, and its analytical expr...
PUM
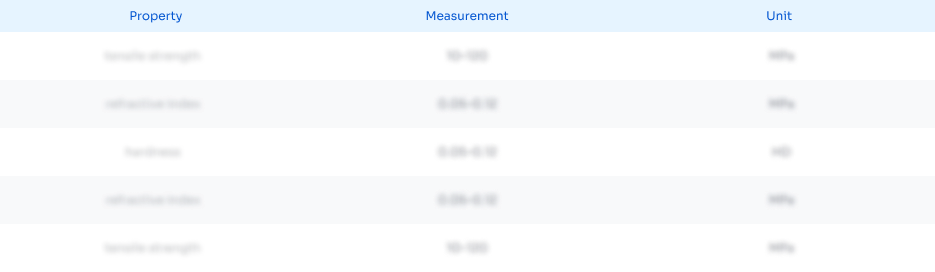
Abstract
Description
Claims
Application Information

- R&D
- Intellectual Property
- Life Sciences
- Materials
- Tech Scout
- Unparalleled Data Quality
- Higher Quality Content
- 60% Fewer Hallucinations
Browse by: Latest US Patents, China's latest patents, Technical Efficacy Thesaurus, Application Domain, Technology Topic, Popular Technical Reports.
© 2025 PatSnap. All rights reserved.Legal|Privacy policy|Modern Slavery Act Transparency Statement|Sitemap|About US| Contact US: help@patsnap.com