Composite material multi-beam box section co-solidifying forming technique
A technology of curing molding and composite materials, applied in the field of composite material autoclave molding process, can solve problems such as poor molding quality, and achieve the effects of shortening the manufacturing cycle, strong repeatability, and simple process operation
- Summary
- Abstract
- Description
- Claims
- Application Information
AI Technical Summary
Problems solved by technology
Method used
Image
Examples
Embodiment 1
[0092] The beam mold assembly for co-curing molding of multi-beam box sections of composite materials includes at least three beam molds arranged side by side; two adjacent beam molds each include a template for clamping beam blanks on adjacent sides, and One of the templates for clamping the beam blank is rigid and the other is flexible.
[0093] Specifically, such as Figure 4 As shown, the beam mold assembly includes a soft outer mold 120 with a rigid panel, and the outer soft mold 120 with a rigid panel is a U-shaped groove body.
[0094] like Figure 8 As shown, the beam mold assembly includes an inner soft mold 130, and the inner soft mold 130 is a cylinder.
[0095] like Figure 8 As shown, the cylinder body of the inner soft mold 130 is provided with a cutaway structure.
[0096] The outer soft mold 120 and the inner soft mold 130 with the rigid plate are both made of a rigid plate 100 connected to flexible plates on both sides. Specifically, such as image 3 As ...
PUM
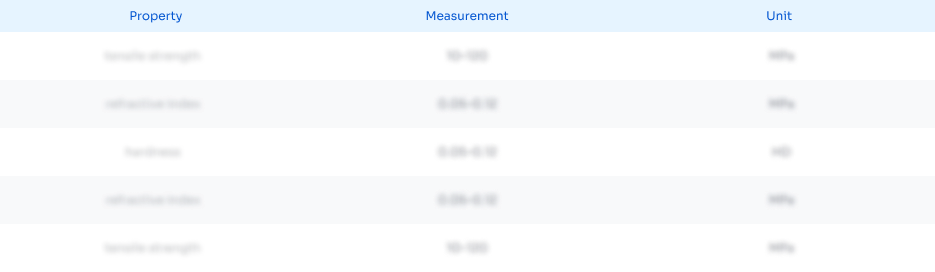
Abstract
Description
Claims
Application Information

- Generate Ideas
- Intellectual Property
- Life Sciences
- Materials
- Tech Scout
- Unparalleled Data Quality
- Higher Quality Content
- 60% Fewer Hallucinations
Browse by: Latest US Patents, China's latest patents, Technical Efficacy Thesaurus, Application Domain, Technology Topic, Popular Technical Reports.
© 2025 PatSnap. All rights reserved.Legal|Privacy policy|Modern Slavery Act Transparency Statement|Sitemap|About US| Contact US: help@patsnap.com