Aluminum oxide roaster vertical fluidized bed and powder flow cooling method
A roaster, alumina technology, applied in fluidized bed furnaces, furnace cooling, furnaces, etc., can solve the problems of inability to recover heat from cooling water, waste of powder energy, etc., to facilitate transportation, ensure product quality, and strengthen heat exchange. Effect
- Summary
- Abstract
- Description
- Claims
- Application Information
AI Technical Summary
Problems solved by technology
Method used
Image
Examples
Embodiment
[0029] Example: see figure 1 with 2 , a vertical fluidized bed for an alumina roaster, comprising a support, a heat exchange unit arranged on the support, and a control system, the heat exchange unit includes at least one heat exchange module, and the heat exchange module is arranged in parallel up and down It consists of heat exchangers, wherein the heat exchange tubes of adjacent heat exchangers are arranged alternately up and down, the upper part of the heat exchange unit is provided with a feeding unit, and the lower part is provided with a discharge valve, and the feeding unit is provided with a high material A level sensor and a low material level sensor, the high material level sensor and the low material level sensor are respectively electrically connected to the controller signal input end of the control system, and the output end of the controller is connected to the discharge valve, which according to the The sampling results of the high material level sensor and t...
Embodiment 2
[0034] Example 2: see image 3 , the structure of embodiment 2 is basically the same as that of embodiment 1, and the similarities will not be repeated. The difference is that a filter plate is arranged below the cloth sieve plate, and the side walls around the filter plate and the cloth sieve plate are all It is fixed on the inner wall of the feed housing, and the housing is provided with a slag removal port for removing the slag on the filter plate, and the slag removal port and the slag removal port for cleaning the cloth sieve plate can be connected It is the same slag removal port, or the slag removal ports can be set separately.
Embodiment 3
[0035] Embodiment 3: The figure is not drawn, and the structure of Embodiment 3 is basically the same as that of Embodiment 1, and the similarities will not be repeated. The difference is that the discharge valve is installed at the lower end of the heat exchange unit through the discharge unit. At the outlet of the outlet, the discharge unit includes an inverted truncated cone-shaped discharge shell and a blanking plate, the upper end of the discharge shell is fixedly connected to the lower end of the heat exchange unit, and the discharge valve is set at the lower end , the blanking plate is provided with a blanking hole opposite to the discharge hole, so that the material flowing on the blanking plate can directly enter the discharge hole through the blanking hole, so as to prevent the accumulation of powder materials.
[0036] The cross-section of the blanking plate is a parabolic shape with an upward opening, or the shape of the blanking plate is a spherical shape with an u...
PUM
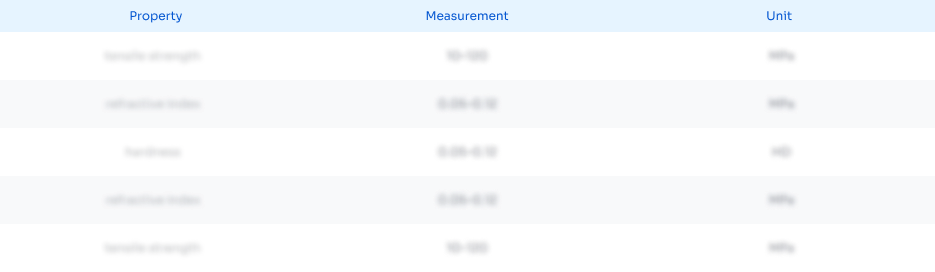
Abstract
Description
Claims
Application Information

- R&D Engineer
- R&D Manager
- IP Professional
- Industry Leading Data Capabilities
- Powerful AI technology
- Patent DNA Extraction
Browse by: Latest US Patents, China's latest patents, Technical Efficacy Thesaurus, Application Domain, Technology Topic, Popular Technical Reports.
© 2024 PatSnap. All rights reserved.Legal|Privacy policy|Modern Slavery Act Transparency Statement|Sitemap|About US| Contact US: help@patsnap.com