Linear motor and compressor
A linear motor, conductive material technology, applied in electrical components, electromechanical devices, electric components, etc., can solve the problems of lateral wear of linear motors, unbalanced mover, mechanical wear, etc., to improve work efficiency, save motor costs, The effect of reducing flux leakage
- Summary
- Abstract
- Description
- Claims
- Application Information
AI Technical Summary
Problems solved by technology
Method used
Image
Examples
Embodiment 1
[0037] In describing the present invention, it is to be understood that the terms "upper", "lower", "front", "rear", "left", "right", "inner", "outer" etc. indicate orientation or position The relationship is based on the orientation or positional relationship shown in the drawings, and is only for the convenience of describing the present invention and simplifying the description, rather than indicating or implying that the referred device or element must have a specific orientation, be constructed and operated in a specific orientation, therefore It should not be construed as a limitation of the present invention.
[0038] Specifically, refer to figure 2 as well as image 3 , the present embodiment provides a linear motor, including a mover 1 and a stator 2, wherein the mover 1 performs reciprocating vibration, and it can have a spring fixed at one end and an output load at the other end (such as a cylinder compressed gas), or both ends can be connected The spring is fixe...
Embodiment 2
[0051] This embodiment further optimizes the structure of the linear motor on the basis of the preferred embodiment 1, specifically, as Figure 8 As shown, the auxiliary magnet 5 is provided at the position corresponding to the tooth portion 211 of the stator core 21 of the magnetic isolating member 4 , that is, the auxiliary magnet 5 is arranged on the tooth portion 41 of the magnetic isolating member. The polarity of one side of the above-mentioned auxiliary magnet 5 is the same as the polarity of the side of the magnet 3 on this side close to the auxiliary magnet 5, which specifically refers to: Figure 10 In the direction shown, when the mover 1 is in the equilibrium position, the two magnets 3 are respectively located on both sides of the auxiliary magnet 5. At this time, the magnetization direction of the auxiliary magnet 5 located above and the direction of magnetization of the auxiliary magnet 5 located below On the contrary, the left side polarity of the auxiliary mag...
Embodiment 3
[0061] This embodiment provides a compressor, specifically a linear compressor, which adopts the linear motor described in the above-mentioned preferred embodiment 1 or preferred embodiment 2, so that its performance has been significantly improved, and its working efficiency has also been improved. improve.
PUM
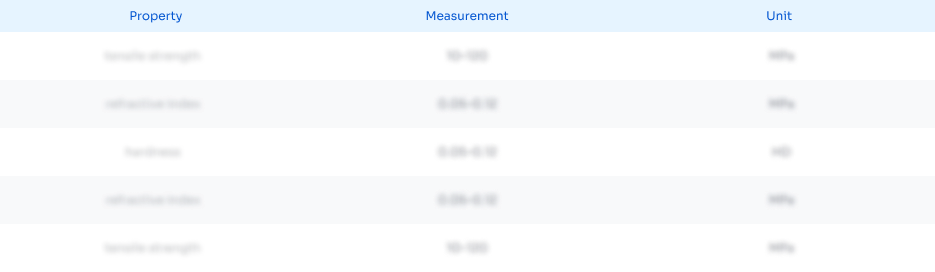
Abstract
Description
Claims
Application Information

- R&D Engineer
- R&D Manager
- IP Professional
- Industry Leading Data Capabilities
- Powerful AI technology
- Patent DNA Extraction
Browse by: Latest US Patents, China's latest patents, Technical Efficacy Thesaurus, Application Domain, Technology Topic, Popular Technical Reports.
© 2024 PatSnap. All rights reserved.Legal|Privacy policy|Modern Slavery Act Transparency Statement|Sitemap|About US| Contact US: help@patsnap.com