Precision calibration method for length of printed labels
A calibration method and label technology, applied in printing devices, printing and other directions, can solve problems such as inability to calibrate, and achieve the effect of reducing printing errors and improving stability
- Summary
- Abstract
- Description
- Claims
- Application Information
AI Technical Summary
Problems solved by technology
Method used
Image
Examples
Embodiment 1
[0033] According to the steps, set the length of the test print to 200mm in the factory mode of the printer, set the printing dot pitch of the stepper motor to 0.125mm and the subdivision drive number of the stepper motor to 4 for the stepper motor controller of the printer, so in When printing a label with a length of 200mm, the stepping motor of the printer needs to act 200*4 / 0.125=6400 times, that is, the total number of signal pulses that need to be sent to control the movement of the motor during printing is 6400.
[0034]In actual printing, the actual length printed by the printer is 195mm, and the difference between the set length and the standard length of 200mm is -5mm. There are 160 pulses included in the difference of -5mm, that is, to correct the difference of -5mm, it is necessary to change 160 pulses out of the total number of 6400 pulses. In order to avoid centralized correction errors, pulses will be used as correction units for adjustments. Then the stepper m...
Embodiment 2
[0037] According to the steps, set the length of the test print to 100mm in the factory mode of the printer, set the printing dot pitch of the stepper motor to 0.05mm and the subdivision drive number of the stepper motor to 8 for the stepper motor controller of the printer, so in When printing a label with a length of 100mm, the stepper motor of the printer needs to operate 100*8 / 0.05=16000 times, that is, the total number of signal pulses that need to be sent to control the movement of the motor is 16000 during printing.
[0038] In actual printing, the actual length printed by the printer is 103mm, and the difference between the set length and the standard length of 100mm is 3mm. There are 480 pulses included in the difference of 3 mm, that is, to correct the difference of 3 mm, it is necessary to change 480 pulses out of the total number of 16000 pulses. In order to avoid centralized correction errors, pulses will be used as correction units for adjustments. Then the stepp...
Embodiment 3
[0041] According to the steps, set the length of the test print to 50mm in the factory mode of the printer, set the printing dot pitch of the stepper motor to 0.1mm and the subdivision drive number of the stepper motor to 2 for the stepper motor controller of the printer, so in When printing a label with a length of 50mm, the stepper motor of the printer needs to operate 50*2 / 0.1=1000 times, that is, the total number of signal pulses that need to be sent to control the movement of the motor during printing is 1000.
[0042] In actual printing, the actual length printed by the printer is 50mm, and the difference between the standard length of 500mm and the set length is 0. Including 0 pulses in the difference value, that is, to correct the difference value of 0, it is necessary to change 0 pulses in the total number of 1000 pulses. The stepping motor is controlled as follows: Since the difference is 0, after any signal pulse is sent within the printing length, the stepping moto...
PUM
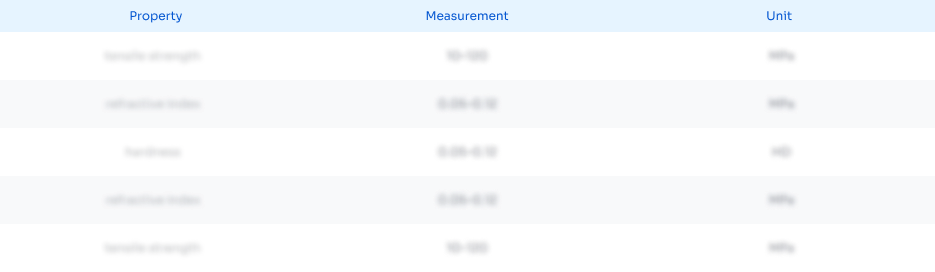
Abstract
Description
Claims
Application Information

- Generate Ideas
- Intellectual Property
- Life Sciences
- Materials
- Tech Scout
- Unparalleled Data Quality
- Higher Quality Content
- 60% Fewer Hallucinations
Browse by: Latest US Patents, China's latest patents, Technical Efficacy Thesaurus, Application Domain, Technology Topic, Popular Technical Reports.
© 2025 PatSnap. All rights reserved.Legal|Privacy policy|Modern Slavery Act Transparency Statement|Sitemap|About US| Contact US: help@patsnap.com