Delayed-coking exhaust gas treatment method
A tail gas treatment and delayed coking technology, applied in chemical instruments and methods, separation methods, water/sludge/sewage treatment, etc., can solve the emulsification problem of sulfur-containing sewage, high oil content and coke powder content affect the operation of downstream devices, etc. problem, to achieve the effect of prolonging the operation cycle and optimizing the venting process
- Summary
- Abstract
- Description
- Claims
- Application Information
AI Technical Summary
Problems solved by technology
Method used
Image
Examples
Embodiment 1
[0036] A method for treating delayed coking tail gas, comprising the following steps: waste gas from a coke tower (a large amount of steam carrying oil and gas) enters the lower part of a steam blowing and venting tower for cooling and oil-water separation, and the upper part of the steam blowing and venting tower is provided with 5 layers of separation trays, The lower part is equipped with 6 layers of baffle trays, the gasoline at the top of the tower is coldly refluxed, the temperature at the top of the tower is 100°C, the temperature at the bottom of the steam blowing and venting tower is 130°C, and the heavy oil at the bottom of the tower is pumped out through the pump at the bottom of the blowing and venting tower and cooled to After 90°C, part of the heavy dirty oil at the bottom of the blowing and venting tower returns to the bottom of the blowing and venting tower, and the other part enters the middle of the blowing and venting tower, and the light dirty oil and sewage ...
Embodiment 2
[0038] A method for treating delayed coking tail gas, comprising the following steps: waste gas from a coke tower (a large amount of steam carrying oil and gas) enters the lower part of a steam-blowing and venting tower for cooling and oil-water separation, and the upper part of the steam-blowing and venting tower is provided with 3 layers of trays, and the lower part is Set up 8-layer trays, cold reflux of gasoline at the top of the tower, the temperature at the top of the tower is 100°C, the temperature at the bottom of the steam blowing and venting tower is 130°C, and the heavy oil at the bottom of the tower is pumped out through the pump at the bottom of the blowing and venting tower and cooled to 90°C by the cooler Part of the heavy dirty oil at the bottom of the steam blowing and venting tower returns to the bottom of the steam blowing and venting tower, and the other part enters the middle of the steam blowing and venting tower, and the light dirty oil and sewage at the t...
Embodiment 3
[0040] A method for treating delayed coking tail gas, comprising the following steps: exhaust gas from a coke tower (a large amount of steam carrying oil and gas) enters the lower part of a steam-blowing and venting tower for cooling and oil-water separation, and the upper part of the steam-blowing and venting tower is provided with 7 layers of trays, and the lower part Set up 5-layer trays, cold reflux of gasoline at the top of the tower, the temperature at the top of the tower is 100°C, the temperature at the bottom of the steam blowing and venting tower is 130°C, and the heavy oil at the bottom of the tower is pumped out through the pump at the bottom of the blowing and venting tower and cooled to 90°C by the cooler Part of the heavy dirty oil at the bottom of the steam blowing and venting tower returns to the bottom of the steam blowing and venting tower, and the other part enters the middle of the steam blowing and venting tower, and the light dirty oil and sewage at the to...
PUM
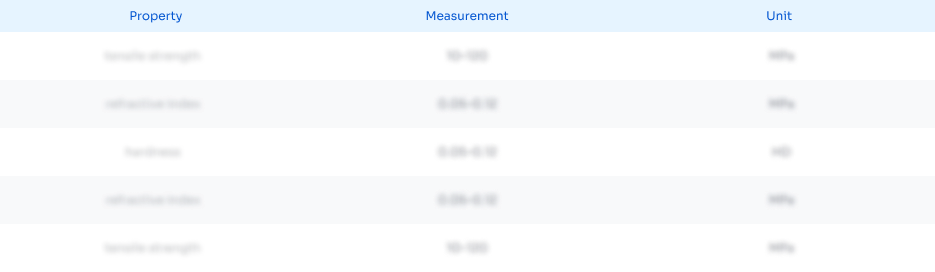
Abstract
Description
Claims
Application Information

- R&D
- Intellectual Property
- Life Sciences
- Materials
- Tech Scout
- Unparalleled Data Quality
- Higher Quality Content
- 60% Fewer Hallucinations
Browse by: Latest US Patents, China's latest patents, Technical Efficacy Thesaurus, Application Domain, Technology Topic, Popular Technical Reports.
© 2025 PatSnap. All rights reserved.Legal|Privacy policy|Modern Slavery Act Transparency Statement|Sitemap|About US| Contact US: help@patsnap.com