Small spacing P2.5 double-layer circuit board manufacturing process
A manufacturing process and circuit board technology, applied in printed circuit manufacturing, printed circuit, photolithography/patterning, etc., can solve the problems of high-frequency signal attenuation, cumbersome process, high production cost, etc., to improve attenuation, simplify the production process, reduce The effect of production costs
- Summary
- Abstract
- Description
- Claims
- Application Information
AI Technical Summary
Problems solved by technology
Method used
Image
Examples
Embodiment Construction
[0022] The technical solution of the present invention will be specifically described below in conjunction with the accompanying drawings.
[0023] A small-pitch P2.5 double-layer circuit board manufacturing process of the present invention comprises the following steps,
[0024] S1: Print the PCB diagram of the light side and the driving side of the small-pitch P2.5 double-layer circuit board to be produced on the thermal transfer paper by laser printer or inkjet printer;
[0025] S2: Stick the printed bottom layer drawing on the copper clad laminate with paper tape, wherein the lamp surface is glued to the bottom layer, the driving surface is glued to the top layer, and positioning holes are drilled on the copper clad laminate;
[0026] S3: Adsorb the toner on the thermal transfer paper to the copper clad board through the thermal transfer machine;
[0027] S4: Wash off the excess copper clad, and complete the production of the small-pitch P2.5 double-layer circuit board. ...
PUM
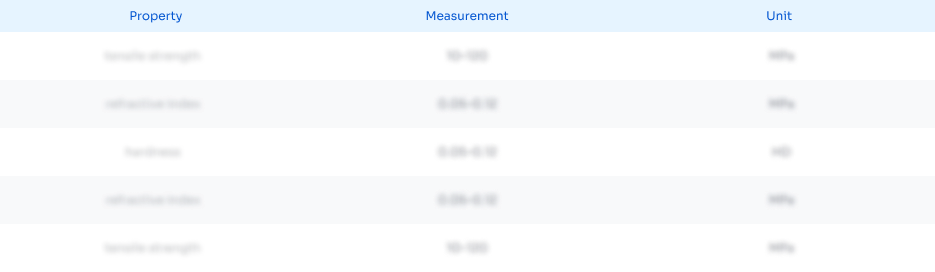
Abstract
Description
Claims
Application Information

- Generate Ideas
- Intellectual Property
- Life Sciences
- Materials
- Tech Scout
- Unparalleled Data Quality
- Higher Quality Content
- 60% Fewer Hallucinations
Browse by: Latest US Patents, China's latest patents, Technical Efficacy Thesaurus, Application Domain, Technology Topic, Popular Technical Reports.
© 2025 PatSnap. All rights reserved.Legal|Privacy policy|Modern Slavery Act Transparency Statement|Sitemap|About US| Contact US: help@patsnap.com