Preparation method of methyl orthoaminobenzoate by means of microchannel reactor
A technology of methyl anthranilate and methyl anthranilate, which is applied in the field of preparing methyl anthranilate by using a microchannel reactor, can solve the problems of low purity and yield of methyl anthranilate, and achieves Good heat and mass transfer effect, no amplification effect, excellent repeatability
- Summary
- Abstract
- Description
- Claims
- Application Information
AI Technical Summary
Problems solved by technology
Method used
Image
Examples
Embodiment 1
[0041] Pump material storage tank A (phthalimide source solution) and material storage tank B (sodium hypochlorite solution) into the microchannel reactor at a volume ratio of 1:1.55. Among them, in material storage tank A (phthalimide source solution), the concentration of phthalimide is 2.3mol / L, the concentration of sodium hydroxide is 4.0mol / L, and the concentration of methanol is 11.0mol / L L. In the B material storage tank (sodium hypochlorite solution), the concentration of the sodium hypochlorite is 13%. The microchannel reactor is composed of MRX, MRH-II and MRH-I connected in series, and the phthalimide source liquid and sodium hypochlorite solution are pumped into the microchannel reactor. The residence time in the microchannel reactor was 30 seconds, and the reaction temperature was -5°C. The reaction solution from the microchannel reactor MRH I was detected, and the conversion rate was 100%, and the mass yield was 89.5%.
Embodiment 2
[0043] Pump material storage tank A (phthalimide source solution) and material storage tank B (sodium hypochlorite solution) into the microchannel reactor at a volume ratio of 1:1.55. Wherein in the A material storage tank (phthalimide source solution), the concentration of phthalimide is 2.3mol / L, the concentration of sodium hydroxide is 2.4mol / L, and the concentration of methanol is 10.5mol / L L. In the B material storage tank (sodium hypochlorite solution), the concentration of the sodium hypochlorite is 13%. The microchannel reactor is composed of MRX, MRH-II and MRH-I connected in series, and the phthalimide source solution and sodium hypochlorite solution are pumped into the microchannel reactor. The residence time in the microchannel reactor was 25 seconds, and the reaction temperature was -5°C. The reaction liquid from the microchannel reactor MRH I was detected, and the conversion rate was 100%, and the mass yield was 85.0%.
Embodiment 3
[0045] A material storage tank (phthalimide source solution) and B material storage tank (sodium hypochlorite solution) are pumped into the microchannel reactor according to a volume ratio of 1:1.55, wherein the A material storage tank (phthalimide amine source solution), the concentration of phthalimide is 4.0mol / L, the concentration of sodium hydroxide is 4.0mol / L, and the concentration of methanol is 11.0mol / L. In the B material storage tank (sodium hypochlorite solution), the concentration of the sodium hypochlorite is 15%. The microchannel reactor is composed of MRX, MRH-II and MRH-I connected in series, and the phthalimide source solution and sodium hypochlorite solution are pumped into the microchannel reactor. The residence time in the microchannel reactor was 23 seconds, and the reaction temperature was -5°C. The reaction liquid from the microchannel reactor MRH I was detected, and the conversion rate was 100%, and the mass yield was 84.3%.
[0046] Table 1 is the re...
PUM
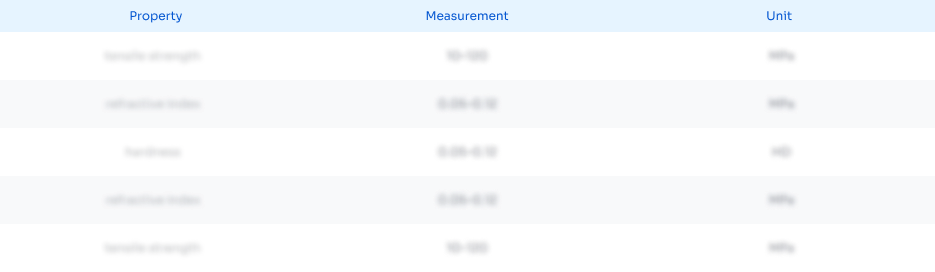
Abstract
Description
Claims
Application Information

- R&D
- Intellectual Property
- Life Sciences
- Materials
- Tech Scout
- Unparalleled Data Quality
- Higher Quality Content
- 60% Fewer Hallucinations
Browse by: Latest US Patents, China's latest patents, Technical Efficacy Thesaurus, Application Domain, Technology Topic, Popular Technical Reports.
© 2025 PatSnap. All rights reserved.Legal|Privacy policy|Modern Slavery Act Transparency Statement|Sitemap|About US| Contact US: help@patsnap.com