Method for preparation of small-particle-size polybutadiene latex
A technology of polybutadiene latex and small particle size, applied in the field of rubber latex production, can solve problems such as long polymerization period, achieve the effects of not decreasing comprehensive performance, improving reaction speed and shortening polymerization time
- Summary
- Abstract
- Description
- Claims
- Application Information
AI Technical Summary
Problems solved by technology
Method used
Examples
Embodiment 1
[0020] 0.25 parts of sodium pyrophosphate (KR) and 0.008 parts of ferrous sulfate (KF) are mixed and complexed before use. The pressure-resistant polymerization kettle was replaced with nitrogen three times, vacuumized, and 165 parts of water, 2.2 parts of potassium oleate, 2 parts of disproportionated rosin soap, and 0.25 parts of electrolyte K were added under negative pressure. 2 CO 3 , 0.45 parts of tertiary dodecyl mercaptan (TDM), 7.5 parts of styrene, 0.2 parts of cumene hydroperoxide (KH), complex solution of sodium pyrophosphate (KR) and ferrous sulfate (KF), 0.35 parts of glucose (KE), finally add 92.5 parts of butadiene, start stirring and heat up, control the temperature of the kettle at 58 ° C, maintain the polymerization reaction for 2 hours, add 0.3 parts of potassium persulfate (KPS), 0.2 parts of ferrous chloride (FeCl 2 ), then continue to react for 3.5 hours, the polymerization pressure is reduced to 0.18MPa, and the polymerization conversion rate reaches 9...
Embodiment 2
[0022] 0.2 parts of sodium pyrophosphate (KR) and 0.008 parts of ferrous sulfate (KF) are mixed and complexed before use. The pressure-resistant polymerization kettle was replaced with nitrogen three times, vacuumized, and 155 parts of water, 2.3 parts of potassium oleate, 2 parts of disproportionated rosin soap, and 0.25 parts of electrolyte K were added under negative pressure. 2 CO 3 , 0.45 parts of tertiary dodecyl mercaptan (TDM), 7.5 parts of styrene, 0.15 parts of cumene hydroperoxide (KH), complex solution of sodium pyrophosphate (KR) and ferrous sulfate (KF), 0.3 parts of glucose (KE), finally add 92.5 parts of butadiene, start stirring and heat up, control the temperature of the kettle at 58.5 ° C, maintain the polymerization reaction for 2.5 hours, add 0.25 parts of potassium persulfate (KPS), 0.3 parts of sodium bisulfite (NaHSO 3 ), then continue to react for 4 hours, the polymerization pressure is reduced to 0.17MPa, the polymerization conversion rate reaches 96...
Embodiment 3
[0024] 0.25 parts of sodium pyrophosphate (KR) and 0.007 parts of ferrous sulfate (KF) are mixed and complexed before use. The pressure-resistant polymerization kettle was replaced with nitrogen three times, vacuumized, and 145 parts of water, 2.2 parts of potassium oleate, 2 parts of disproportionated rosin soap, and 0.25 parts of electrolyte K were added under negative pressure. 2 CO 3 , 0.45 parts of tertiary dodecyl mercaptan (TDM), 7.5 parts of styrene, 0.15 parts of cumene hydroperoxide (KH), complex solution of sodium pyrophosphate (KR) and ferrous sulfate (KF), 0.28 parts of glucose (KE), finally add 92.5 parts of butadiene, start stirring and heat up, control the temperature of the kettle at 58.5°C, maintain the polymerization reaction for 2.5 hours, add 0.20 parts of dibenzoyl peroxide and 0.90 parts of ferrous pyrophosphate, and continue the reaction After 3 hours, the polymerization pressure was reduced to 0.18 MPa, and the polymerization conversion rate reached 9...
PUM
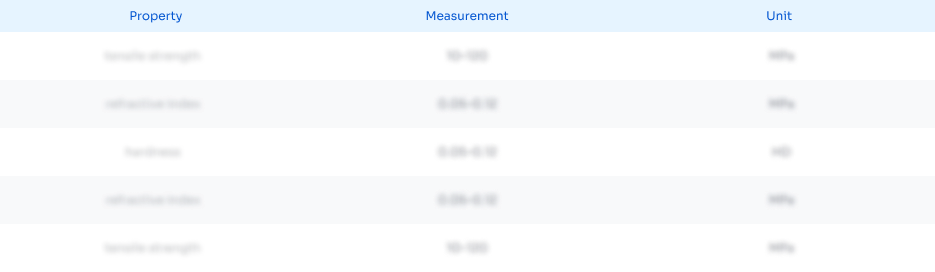
Abstract
Description
Claims
Application Information

- R&D
- Intellectual Property
- Life Sciences
- Materials
- Tech Scout
- Unparalleled Data Quality
- Higher Quality Content
- 60% Fewer Hallucinations
Browse by: Latest US Patents, China's latest patents, Technical Efficacy Thesaurus, Application Domain, Technology Topic, Popular Technical Reports.
© 2025 PatSnap. All rights reserved.Legal|Privacy policy|Modern Slavery Act Transparency Statement|Sitemap|About US| Contact US: help@patsnap.com