Asphaltene thermal plasma cracking processing method
A thermal plasma and cracking treatment technology, which is applied in the field of plasma cracking treatment process, can solve the problems of difficult and efficient utilization and affect the overall benefit of solvent deasphalting, and achieve the effect of improving cooling efficiency and avoiding decomposition reactions
- Summary
- Abstract
- Description
- Claims
- Application Information
AI Technical Summary
Problems solved by technology
Method used
Image
Examples
Embodiment 1
[0024] Asphaltenes produced by heavy oil solvent deasphalting process, in the form of high-temperature liquid phase, pass through CH 4 The atomized transport enters the thermal plasma reactor. The reactor is a down-bed reactor with a diameter of 100 mm and a length of 600 mm. The thermal plasma torch uses hydrogen as the working gas, the input power is 2.0MW, the torch hydrogen flow rate is 75kg / h, the average temperature of the hydrogen plasma exceeds 3000K, and the temperature in the central area is 5000K. The pyrolysis product temperature is 1800K, and the pyrolysis product enters the rapid separation device (the gas-solid separation device disclosed in the prior art patent ZL00105781.2), the gas residence time is 80ms, and the solid phase residence time is 75% of the separation efficiency. The gas separated from the gas outlet, that is, the gas-phase intermediate product, enters the quenching device, and is physically and rapidly cooled by circulating water, and is lowere...
Embodiment 2
[0026] The asphaltenes produced by solvent deasphalting of heavy oil are transported into the thermal plasma reactor through Ar atomization in the form of high-temperature liquid phase. The thermal plasma torch uses hydrogen as the working gas, the input power is 2.5MW, the hydrogen flow rate is 80kg / h, the average temperature of the hydrogen plasma exceeds 3000K, and the temperature in the central area is 6000K. The pyrolysis product temperature is 2000K, and the pyrolysis product enters the rapid separation device (the gas-solid separation device disclosed in the prior art patent ZL00105781.2), the gas residence time is 80ms, and the solid phase residence time is 75% of the separation efficiency. The gas separated from the gas outlet, that is, the gas phase intermediate product, enters the quenching device, is rapidly cooled with propane, and is lowered to room temperature (thereby terminating the thermal decomposition of the product, increasing the content of acetylene in th...
Embodiment 3
[0028] Asphaltenes produced by heavy oil solvent deasphalting process, in the form of high-temperature liquid phase, pass through CH 4 The atomized transport enters the thermal plasma reactor. The thermal plasma torch uses hydrogen as the working gas, the input power is 1.5MW, the hydrogen flow rate of the torch is 70kg / h, the average temperature of the hydrogen plasma exceeds 3000K, and the temperature in the central area is 5000K. The pyrolysis product temperature is 1600K, and the pyrolysis product enters the rapid separation device (the gas-solid separation device disclosed in the prior art patent ZL00105781.2), the gas residence time is 80ms, and the solid phase residence time is 75% of the separation efficiency. The gas separated from the gas outlet, that is, the gas phase intermediate product, enters the quenching device, and is rapidly cooled with a mixture of propane and ethane (50% mole fraction each), and is lowered to room temperature (thus terminating the thermal ...
PUM
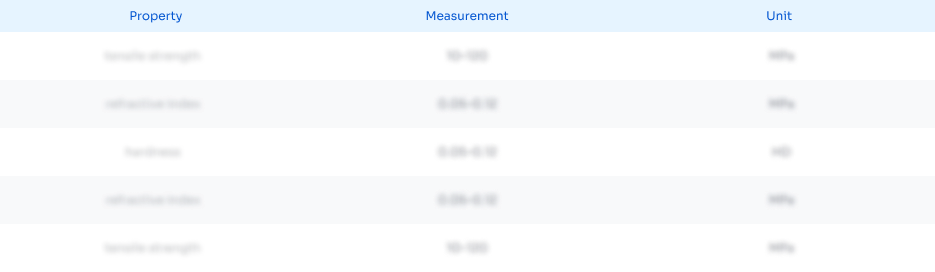
Abstract
Description
Claims
Application Information

- R&D Engineer
- R&D Manager
- IP Professional
- Industry Leading Data Capabilities
- Powerful AI technology
- Patent DNA Extraction
Browse by: Latest US Patents, China's latest patents, Technical Efficacy Thesaurus, Application Domain, Technology Topic, Popular Technical Reports.
© 2024 PatSnap. All rights reserved.Legal|Privacy policy|Modern Slavery Act Transparency Statement|Sitemap|About US| Contact US: help@patsnap.com