Counterbore stamping forming mould and process
A technology of stamping forming and countersinking, which is applied in the direction of metal extrusion dies, perforating tools, forming tools, etc., to achieve the effects of improving the precision of the parts, reducing the cost of mold processing, and improving the life of the mold
- Summary
- Abstract
- Description
- Claims
- Application Information
AI Technical Summary
Problems solved by technology
Method used
Image
Examples
Embodiment Construction
[0033] see figure 1 (a) to figure 1 Shown in (c), a countersink punching forming process of the present invention is divided into two work steps:
[0034] In the first step, the plate-shaped blank 1 is first made into a process part 2 by means of extrusion;
[0035] In the second step, the process part 2 is made into a finished product 3 and a waste material 4 by means of punching and shaping.
[0036] The finished product 3 with counterbore is obtained by two-step forming.
[0037] in:
[0038] 1) The taper angle A2 of process part 2 is 3°-5° larger than the taper angle A3 of the countersunk hole;
[0039] 2) The large end diameter D21 of the frustum hole of process part 2 is 1mm-2mm larger than the large end diameter D31 of the countersunk hole;
[0040] 3) The diameter D2 of the small end of the frustum hole of process part 2 is 1mm-2mm larger than the diameter D3 of the small end of the countersunk hole;
[0041] The extrusion forming process of the first step of the...
PUM
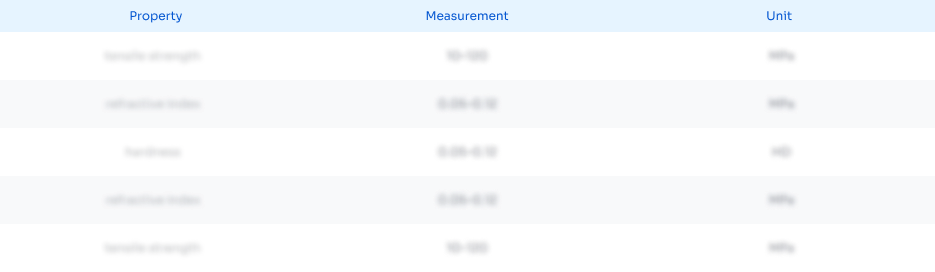
Abstract
Description
Claims
Application Information

- Generate Ideas
- Intellectual Property
- Life Sciences
- Materials
- Tech Scout
- Unparalleled Data Quality
- Higher Quality Content
- 60% Fewer Hallucinations
Browse by: Latest US Patents, China's latest patents, Technical Efficacy Thesaurus, Application Domain, Technology Topic, Popular Technical Reports.
© 2025 PatSnap. All rights reserved.Legal|Privacy policy|Modern Slavery Act Transparency Statement|Sitemap|About US| Contact US: help@patsnap.com