Environment friendly bamboo-charcoal board and manufacturing method thereof
A production method and technology of bamboo charcoal, which is applied in the direction of architecture, building structure, floor, etc., can solve the problems of inability to achieve the use function of furniture panels, inability to automatically degrade, and affect human health, so as to solve human health problems and improve Production conditions, the effect of improving elasticity
- Summary
- Abstract
- Description
- Claims
- Application Information
AI Technical Summary
Problems solved by technology
Method used
Examples
Embodiment 1
[0018] An environmentally friendly bamboo charcoal board, comprising a bamboo charcoal board substrate and a decorative layer arranged on the surface of the bamboo charcoal board substrate. The composition ratio of the bamboo charcoal board substrate is as follows: 40 parts 300 mesh bamboo charcoal powder, 48 parts resin powder, It consists of 2 parts of stabilizer, 3 parts of CPE, 0.5 parts of PE wax, 0.5 parts of grease, 5 parts of foaming regulator and 1 part of foaming agent, and the decorative layer veneer.
[0019] A manufacturing method of environmentally friendly bamboo charcoal board includes the following steps:
[0020] Step 1: Combine 40 parts of 300 mesh bamboo charcoal powder, 48 parts of resin powder, 2 parts of stabilizer, 3 parts of CPE, 0.5 parts of PE wax, 0.5 parts of grease, 5 parts of foaming regulator and 1 part Stir the foaming agent at a temperature of 150°C for 40 minutes, and then pour it into the blender together with high-speed stirring, friction, heati...
Embodiment 2
[0026] An environmentally friendly bamboo charcoal board, comprising a bamboo charcoal board substrate and a decorative layer arranged on the surface of the bamboo charcoal board substrate. The composition ratio of the bamboo charcoal board substrate is as follows: 55 parts of 300 mesh bamboo charcoal powder, 30 parts of resin powder, It consists of 2 parts of stabilizer, 5 parts of CPE, 0.5 parts of PE wax, 0.5 parts of grease, 6 parts of foaming regulator and 1 part of foaming agent, and the decorative layer veneer.
[0027] A manufacturing method of environmentally friendly bamboo charcoal board includes the following steps:
[0028] Step 1: Mix 55 parts of 300 mesh bamboo charcoal powder, 30 parts of resin powder, 2 parts of stabilizer, 5 parts of CPE, 0.5 parts of PE wax, 0.5 parts of grease, 6 parts of foaming regulator and 1 part Stir the foaming agent at 170°C for 30 minutes, and then pour it into the blender together with high-speed stirring, friction, heating and dehumidi...
Embodiment 3
[0034] An environmentally friendly bamboo charcoal board, comprising a bamboo charcoal board substrate and a decorative layer arranged on the surface of the bamboo charcoal board substrate. The composition ratio of the bamboo charcoal board substrate is as follows: 50 parts 300 mesh bamboo charcoal powder, 35 parts resin powder, 3 parts of stabilizer, 4 parts of CPE, 0.5 parts of PE wax, 0.5 parts of grease, 5 parts of foaming regulator and 2 parts of foaming agent, the decorative layer veneer.
[0035] A manufacturing method of environmentally friendly bamboo charcoal board includes the following steps:
[0036] Step 1: Mix 50 parts of 300 mesh bamboo charcoal powder, 35 parts of resin powder, 3 parts of stabilizer, 4 parts of CPE, 0.5 parts of PE wax, 0.5 parts of grease, 5 parts of foaming regulator and 2 parts Stir the foaming agent at a temperature of 200°C for 25 minutes, and then pour it into the blender together with high-speed stirring, friction heating and dehumidificatio...
PUM
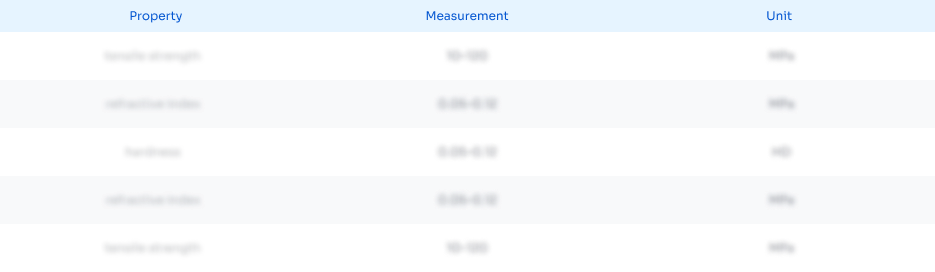
Abstract
Description
Claims
Application Information

- R&D
- Intellectual Property
- Life Sciences
- Materials
- Tech Scout
- Unparalleled Data Quality
- Higher Quality Content
- 60% Fewer Hallucinations
Browse by: Latest US Patents, China's latest patents, Technical Efficacy Thesaurus, Application Domain, Technology Topic, Popular Technical Reports.
© 2025 PatSnap. All rights reserved.Legal|Privacy policy|Modern Slavery Act Transparency Statement|Sitemap|About US| Contact US: help@patsnap.com