Electropolishing treatment method for stainless steel
A treatment method and electrolytic polishing technology, applied in the field of stainless steel processing, can solve the problems affecting the surface quality of polished workpieces, affecting stainless steel processing, and high temperature requirements, and achieve the effect of improving polishing quality, reducing pits, and facilitating accumulation.
- Summary
- Abstract
- Description
- Claims
- Application Information
AI Technical Summary
Problems solved by technology
Method used
Examples
Embodiment 1
[0022] An electrolytic polishing treatment method for stainless steel, comprising the steps of:
[0023] (1) Cleaning and degreasing:
[0024] Rinse the impurities on the surface of the stainless steel with clean water first, then put it into the industrial degreasing liquid, heat it to keep the temperature of the degreasing liquid at 42°C, stir continuously for 7 minutes, take out the stainless steel, rinse it with clean water again and reserve it use;
[0025] (2) Electrolyte preparation:
[0026] a. Electrolyte A preparation, first weigh the following materials by weight: 14 parts of sulfuric acid, 6 parts of phosphoric acid, 1 part of sodium nitrate, 1 part of sodium tartrate, 13 parts of polyvinyl alcohol, 3 parts of sodium alginate, 0.3 part of permanganese Potassium acid potassium, 0.2 part of polyacrylamide, 0.4 part of glycerin, 105 parts of distilled water; then the above-mentioned material components were mixed together, and the electrolyte A was obtained after st...
Embodiment 2
[0036] An electrolytic polishing treatment method for stainless steel, comprising the steps of:
[0037] (1) Cleaning and degreasing:
[0038] Rinse the impurities on the surface of the stainless steel with clean water first, then put it into the industrial degreasing liquid, heat it to keep the temperature of the degreasing liquid at 44°C, stir continuously for 9 minutes, take out the stainless steel, rinse it with clean water again and reserve it use;
[0039] (2) Electrolyte preparation:
[0040] a. Electrolyte A preparation, first weigh the following materials by weight: 17 parts of sulfuric acid, 8 parts of phosphoric acid, 2 parts of sodium nitrate, 2 parts of sodium tartrate, 15 parts of polyvinyl alcohol, 5 parts of sodium alginate, 0.5 part of permanganese potassium nitrite, 0.4 part of polyacrylamide, 0.6 part of glycerin, 110 parts of distilled water; then the above-mentioned material components were mixed together, and the electrolyte A was obtained after stirrin...
PUM
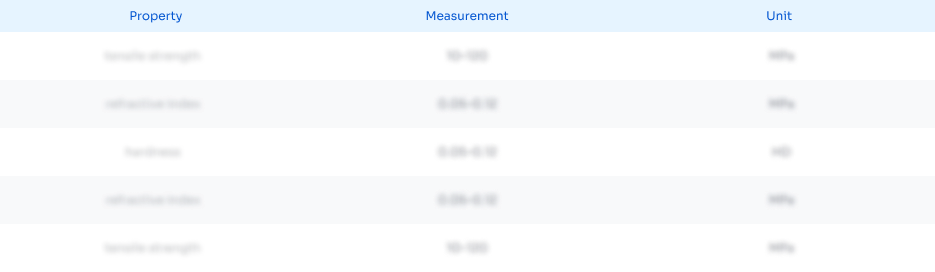
Abstract
Description
Claims
Application Information

- R&D Engineer
- R&D Manager
- IP Professional
- Industry Leading Data Capabilities
- Powerful AI technology
- Patent DNA Extraction
Browse by: Latest US Patents, China's latest patents, Technical Efficacy Thesaurus, Application Domain, Technology Topic, Popular Technical Reports.
© 2024 PatSnap. All rights reserved.Legal|Privacy policy|Modern Slavery Act Transparency Statement|Sitemap|About US| Contact US: help@patsnap.com