Technological method for synthesizing ketoxime
A process method and a technology for synthesizing ketoxime, applied in oxime preparation, organic chemistry, etc., can solve problems such as dissolution and loss of catalyst active elements, impact on catalyst recycling, unreasonable raw material reaction ratio, etc., to avoid pollution and separation problems, The effect of improving material utilization and improving stability
- Summary
- Abstract
- Description
- Claims
- Application Information
AI Technical Summary
Problems solved by technology
Method used
Image
Examples
Embodiment 1
[0032] First configure NaHCO with pH=10 3 Add 50g of aqueous solution into the three-necked flask, then add 2g of TS-1 catalyst, 80g of cyclohexanone in sequence, and the temperature of the water bath is 50°C. Insert the pH meter detection electrode, start stirring, and feed ammonia and hydrogen peroxide at the same time. 10g, the feeding time is 1 hour, the rate of passing hydrogen peroxide is kept at 1.2:1 with the molar ratio of ammonia water, until the pH value is restored from 12 during the reaction to the initial pH value = 10, continue to keep warm for 5 hours, and stop the reaction. After cooling to room temperature, the upper light phase is taken out to obtain the product oxime, part of the lower water phase is released, and 70% of the water is removed by rotary evaporation, and then returned to the reactor to continue recycling. The gas chromatogram of its product is shown in figure 1 .
Embodiment 2
[0034] First configure NaHCO with pH=9 3 Add 50g of aqueous solution into the three-necked flask, then add 2g of TS-1 catalyst, 87g of acetone in sequence, the temperature of the water bath is 70°C, insert the detection electrode of the pH meter, start stirring, and feed ammonia gas and hydrogen peroxide at the same time, the amount of ammonia gas feeding is 10g , the feeding time is 1 hour, the rate of passing hydrogen peroxide is kept at 1.2:1 with the molar amount of ammonia water, until the pH value is restored from 12 in the reaction process to the initial pH value = 9, continue to keep warm for 5 hours, and stop the reaction. After cooling to room temperature, the upper light phase is taken out to obtain the product oxime, part of the lower water phase is released, and 70% of the water is removed by rotary evaporation, and then returned to the reactor to continue recycling.
Embodiment 3
[0036] First configure Na with pH=12 2 CO 3 Add 50g of aqueous solution into the three-necked flask, then add 2g of TS-1 catalyst, 90g of methyl ethyl ketone in sequence, the temperature of the water bath is 50°C, insert the pH meter detection electrode, start stirring, and feed ammonia and hydrogen peroxide at the same time, the amount of ammonia gas is 10g, the feeding time is 1 hour, the rate of passing hydrogen peroxide is kept at 1.2:1 with the molar amount of ammonia water, until the pH value returns from 13 during the reaction to the initial pH value = 12, continue to keep warm for 5 hours, and stop the reaction. After cooling to room temperature, the upper light phase is taken out to obtain the product oxime, part of the lower water phase is released, and 70% of the water is removed by rotary evaporation, and then returned to the reactor to continue recycling.
PUM
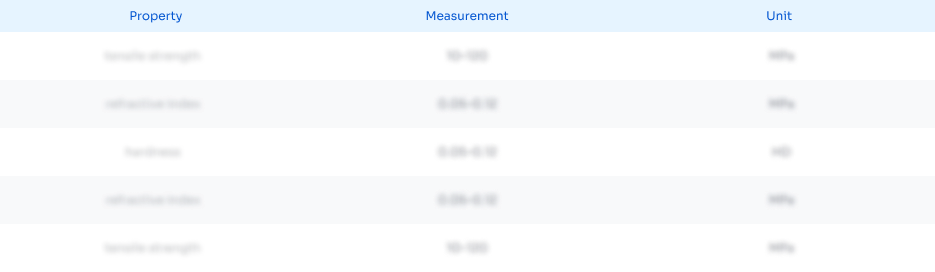
Abstract
Description
Claims
Application Information

- R&D
- Intellectual Property
- Life Sciences
- Materials
- Tech Scout
- Unparalleled Data Quality
- Higher Quality Content
- 60% Fewer Hallucinations
Browse by: Latest US Patents, China's latest patents, Technical Efficacy Thesaurus, Application Domain, Technology Topic, Popular Technical Reports.
© 2025 PatSnap. All rights reserved.Legal|Privacy policy|Modern Slavery Act Transparency Statement|Sitemap|About US| Contact US: help@patsnap.com