Method for determining modal finite element simulation precision of mechanical part
A technology for mechanical parts and determination methods, applied in design optimization/simulation, special data processing applications, instruments, etc., can solve problems such as inaccurate comparison results and inability to define simulation accuracy, achieve accurate and reliable elastic-plastic data, and avoid calculation. The effect of excessive volume and accurate results
- Summary
- Abstract
- Description
- Claims
- Application Information
AI Technical Summary
Problems solved by technology
Method used
Image
Examples
Embodiment Construction
[0047] The present invention will be described in detail below with reference to the accompanying drawings and specific embodiments. This embodiment is implemented on the premise of the technical solution of the present invention, and provides a detailed implementation manner and a specific operation process, but the protection scope of the present invention is not limited to the following embodiments.
[0048] like figure 1 As shown, this embodiment provides a method for determining the modal finite element simulation accuracy of a simple cantilever arm, including the following steps:
[0049] 1) Determine the material of the cantilever arm, prepare material splines and carry out spline experiments to obtain elastic-plastic data such as elastic modulus and stress-strain curves of multiple groups of materials. Tensile conditions, and finally 20 sets of tensile experiments were carried out;
[0050] 2) as figure 2 As shown, the design of experiments (DOE) method is used to ...
PUM
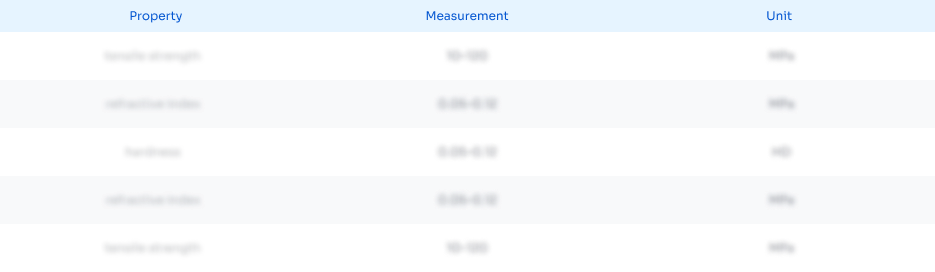
Abstract
Description
Claims
Application Information

- Generate Ideas
- Intellectual Property
- Life Sciences
- Materials
- Tech Scout
- Unparalleled Data Quality
- Higher Quality Content
- 60% Fewer Hallucinations
Browse by: Latest US Patents, China's latest patents, Technical Efficacy Thesaurus, Application Domain, Technology Topic, Popular Technical Reports.
© 2025 PatSnap. All rights reserved.Legal|Privacy policy|Modern Slavery Act Transparency Statement|Sitemap|About US| Contact US: help@patsnap.com