Printing and dyeing process of polyester-cotton blended fabric
A printing and dyeing process, polyester cotton technology, applied in the direction of dyeing, textiles and papermaking, fiber types, etc., can solve the problems of high fabric defect rate, uneven dyeing, fading, etc., and achieve enhanced dye adhesion and uniform dyeing Effect
- Summary
- Abstract
- Description
- Claims
- Application Information
AI Technical Summary
Problems solved by technology
Method used
Examples
Embodiment 1
[0021] A printing and dyeing process for polyester-cotton blended fabrics specifically includes the following steps:
[0022] (1) Pretreatment: decoct the cloth with brine of saturated concentration at 60°C for 10 minutes, then cover the cloth with vinegar lees at 43°C and maintain the temperature for 24-36 hours, then wash the cloth with deionized water;
[0023] (2) Pretreatment: Immerse the cloth in a pretreatment tank with a pretreatment liquid, and control the bath ratio in the pretreatment tank to be 2:3 to 6;
[0024] (3) Dyeing: put the fabric in the water-soluble chitosan solution, put 0.1% methylene blue by weight of the fabric into the solution after 30 minutes, put cationic blue SD-BL 100% by weight of 0.2% into the solution after 2 hours (B-159), then the solution is heated to 53-61°C, the dye liquor of 40% of the fabric weight is put into the solution, then the temperature is lowered to 10°C at a rate of 1-2°C / min, and the fabric weight is put into the solution ...
Embodiment 2
[0031] A printing and dyeing process for polyester-cotton blended fabrics specifically includes the following steps:
[0032] (1) Pretreatment: decoct the cloth with brine of saturated concentration at 60°C for 10 minutes, then cover the cloth with vinegar lees at 43°C and maintain the temperature for 24-36 hours, then wash the cloth with deionized water;
[0033] (2) Pretreatment: Immerse the cloth in a pretreatment tank with a pretreatment liquid, and control the bath ratio in the pretreatment tank to be 2:3 to 6;
[0034] (3) Dyeing: put the fabric in the water-soluble chitosan solution, put 0.1% methylene blue by weight of the fabric into the solution after 30 minutes, put cationic blue SD-BL 100% by weight of 0.2% into the solution after 2 hours (B-159), then the solution is heated to 53-61°C, the dye liquor of 40% of the fabric weight is put into the solution, then the temperature is lowered to 10°C at a rate of 1-2°C / min, and the fabric weight is put into the solution ...
Embodiment 3
[0041] A printing and dyeing process for polyester-cotton blended fabrics specifically includes the following steps:
[0042] (1) Pretreatment: decoct the cloth with brine of saturated concentration at 60°C for 10 minutes, then cover the cloth with vinegar lees at 43°C and maintain the temperature for 24-36 hours, then wash the cloth with deionized water;
[0043] (2) Pretreatment: Immerse the cloth in a pretreatment tank with a pretreatment liquid, and control the bath ratio in the pretreatment tank to be 2:3 to 6;
[0044] (3) Dyeing: put the fabric in the water-soluble chitosan solution, put 0.1% methylene blue by weight of the fabric into the solution after 30 minutes, put cationic blue SD-BL 100% by weight of 0.2% into the solution after 2 hours (B-159), then the solution is heated to 53-61°C, the dye liquor of 40% of the fabric weight is put into the solution, then the temperature is lowered to 10°C at a rate of 1-2°C / min, and the fabric weight is put into the solution ...
PUM
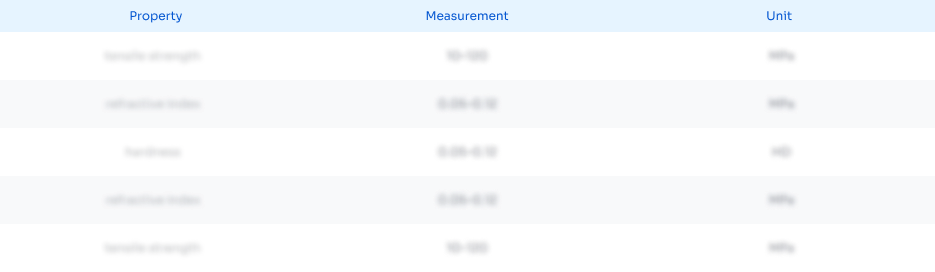
Abstract
Description
Claims
Application Information

- R&D
- Intellectual Property
- Life Sciences
- Materials
- Tech Scout
- Unparalleled Data Quality
- Higher Quality Content
- 60% Fewer Hallucinations
Browse by: Latest US Patents, China's latest patents, Technical Efficacy Thesaurus, Application Domain, Technology Topic, Popular Technical Reports.
© 2025 PatSnap. All rights reserved.Legal|Privacy policy|Modern Slavery Act Transparency Statement|Sitemap|About US| Contact US: help@patsnap.com