Cobalt salt black chemical oxidation solution for aluminum and aluminum alloy and application thereof
A chemical oxidation, aluminum alloy technology, applied in the direction of metal material coating technology, can solve the problems of short service life of blackening solution, high production cost, poor method stability, etc., to achieve improved appearance compactness, good film-forming effect, The effect of a good blackening effect
- Summary
- Abstract
- Description
- Claims
- Application Information
AI Technical Summary
Problems solved by technology
Method used
Image
Examples
Embodiment 1-4
[0021] Examples 1-4: Blackening solutions containing different cobalt salts (without dispersants and additives) and their blackening experiments.
[0022]
[0023] Select 4 different cobalt salt formulas to carry out parallel experiments, and keep other components and dosages in the formulas exactly the same. Through the following process flow, 4 kinds of black chemical oxidation solutions are compared and analyzed:
[0024] (1) Preprocessing:
[0025] Pickling and alkali cleaning are carried out on the surface of the aluminum sheet to remove the formed oxide film and stains.
[0026] (2) Chemical oxidation:
[0027] A) Preparation of blackening solution: Accurately weigh various solid components according to the dosage in the above table, put them in a beaker and add water to 1L after weighing, stir and dissolve, place in a water bath and heat to 80°C, adjust with nitric acid until the pH of the solution is 1-3.
[0028] B) Oxidation film formation: put the pretreated ...
Embodiment 5-8
[0030] Examples 5-8: Blackening solutions containing different dispersants (without additives) and their blackening experiments.
[0031]
[0032]
[0033] Select 4 different dispersants to conduct parallel experiments, and keep the other components and dosages in the formula exactly the same. Through the following process flow, 4 kinds of black chemical oxidation solutions are compared and analyzed:
[0034] (1) Preprocessing:
[0035] Pickling and alkali cleaning are carried out on the surface of the aluminum sheet to remove the formed oxide film and stains.
[0036] (2) Chemical oxidation:
[0037] A) Preparation of blackening solution: Accurately weigh various solid components according to the dosage in the above table, put them in a beaker and add water to 1L after weighing, stir and dissolve, place in a water bath and heat to 80°C, adjust with nitric acid until the pH of the solution is 1-3.
[0038] B) Oxidation film formation: put the pretreated aluminum shee...
Embodiment 9-12
[0040] Examples 9-12: Blackening solutions containing different additives (without dispersant) and their blackening experiments.
[0041]
[0042] Choose 4 kinds of different additives to carry out parallel experiment, and keep other components and dosage in the formula exactly the same. Through the following process flow, 4 kinds of black chemical oxidation solutions are compared and analyzed:
[0043] (1) Preprocessing:
[0044] Pickling and alkali cleaning are carried out on the surface of the aluminum sheet to remove the formed oxide film and stains.
[0045] (2) Chemical oxidation:
[0046] A) Preparation of blackening solution: Accurately weigh various solid components according to the dosage in the above table, put them in a beaker and add water to 1L after weighing, stir and dissolve, place in a water bath and heat to 80°C, adjust with nitric acid until the pH of the solution is 1-3.
[0047] B) Oxidation film formation: put the pretreated aluminum sheet in the bl...
PUM
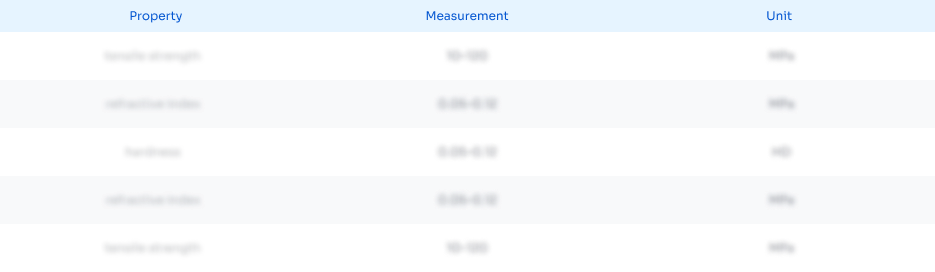
Abstract
Description
Claims
Application Information

- R&D
- Intellectual Property
- Life Sciences
- Materials
- Tech Scout
- Unparalleled Data Quality
- Higher Quality Content
- 60% Fewer Hallucinations
Browse by: Latest US Patents, China's latest patents, Technical Efficacy Thesaurus, Application Domain, Technology Topic, Popular Technical Reports.
© 2025 PatSnap. All rights reserved.Legal|Privacy policy|Modern Slavery Act Transparency Statement|Sitemap|About US| Contact US: help@patsnap.com