Preparation process of stainless steel wire
A technology of stainless steel wire and preparation process, applied in the field of preparation technology of stainless steel wire, can solve the problems of occupying a large area, unfavorable to the expansion of enterprise production capacity, increasing transportation costs, etc., to achieve stable water temperature fluctuations, improve market competitiveness, and save money. The effect of factory space
- Summary
- Abstract
- Description
- Claims
- Application Information
AI Technical Summary
Problems solved by technology
Method used
Image
Examples
Embodiment Construction
[0052] see Figure 1~4 , a kind of preparation technology of stainless steel wire that the present invention relates to, described technology comprises the following steps:
[0053] Step 1. Use an online film drying device to coat the wire with a film agent and dry it;
[0054] Step 2. Lead the wire into the rough-drawing straight-forward wire drawing machine and draw it continuously for 3 to 5 times;
[0055] Step 3, surface heat treatment, import the drawn wire into a heat treatment furnace for surface brightening treatment, at this time, the heating temperature in the heat treatment furnace is 1080±10°C; the forward speed of the wire is 5~6m / min; Water cooling, washing and drying;
[0056] Step 4, using an online film drying device to coat and dry the wire rod after step 3;
[0057] Step 5. Lead the wire into the fine-drawing straight-in wire drawing machine and draw it continuously for 3 to 5 times;
[0058] Step 6, surface heat treatment, import the drawn wire into a ...
PUM
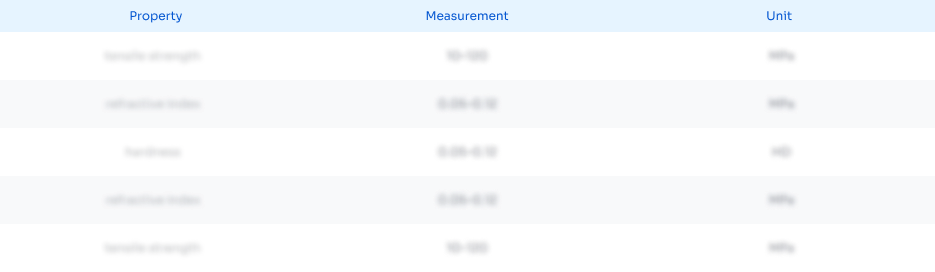
Abstract
Description
Claims
Application Information

- R&D
- Intellectual Property
- Life Sciences
- Materials
- Tech Scout
- Unparalleled Data Quality
- Higher Quality Content
- 60% Fewer Hallucinations
Browse by: Latest US Patents, China's latest patents, Technical Efficacy Thesaurus, Application Domain, Technology Topic, Popular Technical Reports.
© 2025 PatSnap. All rights reserved.Legal|Privacy policy|Modern Slavery Act Transparency Statement|Sitemap|About US| Contact US: help@patsnap.com