A kind of method that magnesium-aluminum-lanthanum composite oxide catalyzes synthetic ethyl methyl carbonate
A technology of ethyl methyl carbonate and composite oxides, applied in chemical instruments and methods, organic carbonate preparation, physical/chemical process catalysts, etc., can solve problems such as difficult large-scale application, complicated preparation process, and high price, and achieve Easy separation, good selectivity and low cost
- Summary
- Abstract
- Description
- Claims
- Application Information
AI Technical Summary
Problems solved by technology
Method used
Examples
Embodiment 1
[0020] Catalyst preparation: 0.3 mol magnesium chloride, 0.12 mol aluminum chloride and 0.03 mol lanthanum chloride were prepared into 300 mL of aqueous solution A; 0.75 mol of sodium hydroxide and 0.23 mol of sodium carbonate were prepared into 300 mL of aqueous solution B; at a constant temperature of 40 Under the condition of constant stirring, add solution A and solution B into 100 mL water at the same speed, keep the pH of the mixed solution = 9-11, react for 0.5 h, crystallize at 90 °C for 15 h; filter, wash and dry , after pulverization, the magnesium aluminum lanthanum hydrotalcite Mg 2 + 2 / 3 Al 3+ 4 / 15 La 3+ 1 / 15 (OH) 2 (CO 3 2- ) 1 / 6 4H 2 O; The resulting magnesium-aluminum-lanthanum hydrotalcites were calcined at 400°C for 6 h to obtain magnesium-aluminum-lanthanum composite oxides.
Embodiment 2
[0022] Catalyst preparation: 0.4 mol magnesium nitrate, 0.05 mol aluminum nitrate and 0.05 mol lanthanum nitrate were prepared into 800 mL aqueous solution A; 0.9 mol sodium hydroxide and 0.12 mol sodium carbonate were prepared into 800 mL aqueous solution B; And under the condition of continuous stirring, add solution A and solution B into 100mL water at the same speed, keep the mixed solution pH=9~11, react for 2 hours, and crystallize at 120°C for 8 hours; after filtering, washing, drying and crushing , to obtain magnesium aluminum lanthanum hydrotalcite Mg 2+ 0.8 Al 3 + 0.1 La 3+ 0.1 (OH) 2 (CO 3 2- ) 0.1 ·8H 2 O; The resulting hydrocalumite was calcined at 500°C for 4 h to obtain the magnesium-aluminum-lanthanum composite oxide.
Embodiment 3
[0024] Catalyst preparation: Prepare 200 mL of aqueous solution A with 0.2 mol of magnesium sulfate, 0.18 mol of aluminum sulfate and 0.02 mol of lanthanum sulfate; prepare 200 mL of aqueous solution B with 0.56 mol of sodium hydroxide and 0.18 mol of sodium carbonate; Under the condition of continuous stirring, add solution A and solution B into 100 mL water at the same speed, keep the pH of the mixed solution at 9~11, react for 2 h, and crystallize at 150°C for 4 h; filter, wash, dry, After pulverization, magnesium aluminum lanthanum hydrotalcite Mg is obtained 2+ 0.5 Al 3+ 0.45 La 3+ 0.05 (OH) 2 (CO 3 2- ) 0.252H 2 O; The resulting hydrocalumite was calcined at 600°C for 2 h to obtain the magnesium-aluminum-lanthanum composite oxide.
PUM
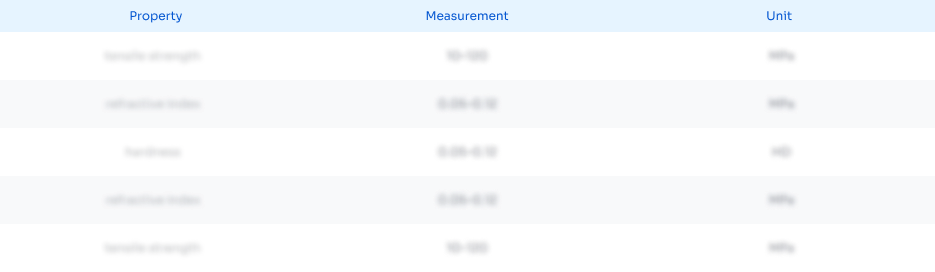
Abstract
Description
Claims
Application Information

- Generate Ideas
- Intellectual Property
- Life Sciences
- Materials
- Tech Scout
- Unparalleled Data Quality
- Higher Quality Content
- 60% Fewer Hallucinations
Browse by: Latest US Patents, China's latest patents, Technical Efficacy Thesaurus, Application Domain, Technology Topic, Popular Technical Reports.
© 2025 PatSnap. All rights reserved.Legal|Privacy policy|Modern Slavery Act Transparency Statement|Sitemap|About US| Contact US: help@patsnap.com