A Method for Evaluating the Loose State of the Support of the Rotor-Bearing System
A state assessment and system dynamics technology, applied in the testing of machine/structural components, testing of mechanical components, instruments, etc., can solve problems such as the evaluation of looseness without support, to prevent catastrophic accidents, prevent large gaps from loosening, Guaranteed effect of accuracy and reliability
- Summary
- Abstract
- Description
- Claims
- Application Information
AI Technical Summary
Problems solved by technology
Method used
Image
Examples
example
[0101] Select the rotor-sliding bearing as the calculation object, as follows:
[0102] In view of the strong nonlinear dynamic behavior that can be produced by the rotor-sliding bearing system, this paper uses the Runge-Kutta method with 4-5 step variable step size to simulate and calculate the dynamic model without loosening and the loosening dynamic model with support respectively. In order to ensure the convergence of the solution and reduce calculation errors, the integration step size and other parameters are selected in the simulation as h=π / 512; e=0.5×10 -4 m; m 1 = 32.1 kg; m 2 = 4kg; m 3 =10kg; k=2.5×10 7 N / m; k b1 =7.5×10 9 N / m; k b3 =7.5×10 7 N / m; c 1 =1050N·s / m; c 2 =2100N·s / m; c b1 =350N·s / m; c b2 =100N·s / m; c b3 =500N·s / m.
[0103] Take X=[x 1 ,y 1 ,x 2 ,y 2 ,x 3 ,y 3 ,y 4 ] is processed as follows, X'=X / c, X'=X' / (cω), X'=X' / (cω 2 ), where c is the average thickness of the lubricating film, and ω is the angular velocity of the shaft. Under ...
PUM
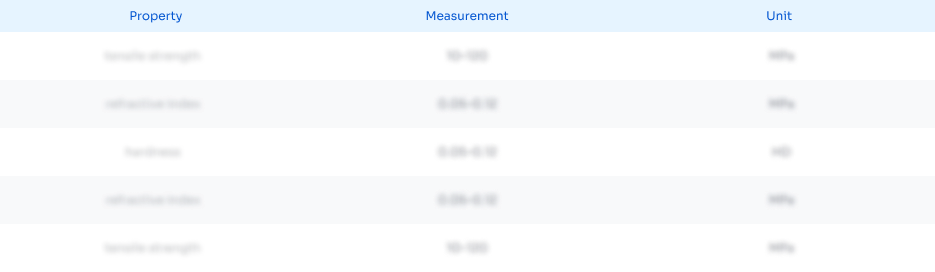
Abstract
Description
Claims
Application Information

- R&D Engineer
- R&D Manager
- IP Professional
- Industry Leading Data Capabilities
- Powerful AI technology
- Patent DNA Extraction
Browse by: Latest US Patents, China's latest patents, Technical Efficacy Thesaurus, Application Domain, Technology Topic, Popular Technical Reports.
© 2024 PatSnap. All rights reserved.Legal|Privacy policy|Modern Slavery Act Transparency Statement|Sitemap|About US| Contact US: help@patsnap.com