A passive dynamic leveling control system of hydraulic press and its control method
A control system and hydraulic press technology, applied in the direction of presses, manufacturing tools, etc., can solve the problems of electro-hydraulic proportional dynamic leveling control system manufacturing, high maintenance costs, poor anti-interference ability, and difficult control
- Summary
- Abstract
- Description
- Claims
- Application Information
AI Technical Summary
Problems solved by technology
Method used
Image
Examples
Embodiment Construction
[0055] The present invention will be further described below in conjunction with the accompanying drawings and specific embodiments.
[0056] Such as image 3 As shown, a passive dynamic leveling control system of a hydraulic machine in this embodiment, the hydraulic machine body includes a main system oil tank 1, an upper beam 2, a master cylinder 3, a first leveling hydraulic cylinder 5, and a second leveling hydraulic cylinder 7. The third leveling hydraulic cylinder 8, the fourth leveling hydraulic cylinder 9, the return cylinder 11, the movable beam 4 and the lower beam 6, the main system oil tank 1 is installed on the upper end of the upper beam 2, and the main cylinder 3 and the return cylinder 11 are composed of The main system controls and jointly drives the movable beam 4 to realize reciprocating motion between the upper beam 2 and the lower beam 6, the first leveling hydraulic cylinder 5, the second leveling hydraulic cylinder 7, the third leveling hydraulic cylinde...
PUM
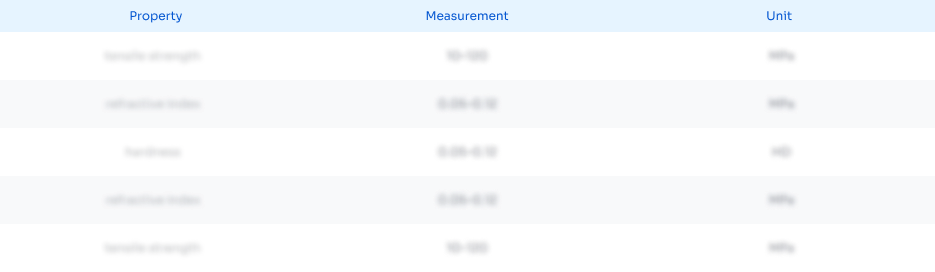
Abstract
Description
Claims
Application Information

- R&D
- Intellectual Property
- Life Sciences
- Materials
- Tech Scout
- Unparalleled Data Quality
- Higher Quality Content
- 60% Fewer Hallucinations
Browse by: Latest US Patents, China's latest patents, Technical Efficacy Thesaurus, Application Domain, Technology Topic, Popular Technical Reports.
© 2025 PatSnap. All rights reserved.Legal|Privacy policy|Modern Slavery Act Transparency Statement|Sitemap|About US| Contact US: help@patsnap.com