Acyl chloride co-production method
A technology of acryloyl chloride and process method, which is applied in chemical instruments and methods, preparation of acyl halide, preparation of carboxylate, etc., which can solve problems such as difficult separation and treatment, low yield, large amount of acid waste discharge, etc.
- Summary
- Abstract
- Description
- Claims
- Application Information
AI Technical Summary
Problems solved by technology
Method used
Image
Examples
Embodiment 1
[0023] 47.4 grams of 1,3,5-trimethyl-2-(trichloromethyl)-benzene, 0.15 grams of ferric chloride, and 0.25 grams of 2,6-di-tert-butyl-4-methylphenol Place in a reaction flask, heat to 105°C, add 14.4 grams of acrylic acid dropwise, and distill the generated acryloyl chloride while adding dropwise, and absorb the generated hydrogen chloride gas with water, add the acrylic acid dropwise in about 1 hour, and then slowly raise the temperature The acryloyl chloride was distilled off steadily at 180° C. to obtain 12.8 g of acryloyl chloride, and then 33.8 g of 2,4,6-trimethylbenzoyl chloride were obtained by distillation under reduced pressure.
Embodiment 2
[0025] 47.4 grams of 1,3,5-trimethyl-2-(trichloromethyl)-benzene, 0.1 grams of zinc oxide, and 0.25 grams of 2,6-di-tert-butyl-4-methylphenol In the reaction flask, heat to 105°C, add 14.4 grams of acrylic acid dropwise, distill off the generated acryloyl chloride while adding dropwise, absorb the generated hydrogen chloride gas with water, finish adding the acrylic acid dropwise in about 1 hour, and then slowly raise the temperature to At 180°C, acryloyl chloride was distilled out steadily to obtain 12.5 g of acryloyl chloride, and then 30.8 g of 2,4,6-trimethylbenzoyl chloride were obtained by distillation under reduced pressure.
Embodiment 3
[0027] 47.4 grams of 1,3,5-trimethyl-2-(trichloromethyl)-benzene, 0.34 grams of anhydrous aluminum chloride, and 0.26 grams of 2,6-di-tert-butyl-4- Place methyl phenol in a reaction flask, heat it to 125°C, add 14.4 grams of methacrylic acid dropwise, distill off the generated acryloyl chloride while adding dropwise, absorb the generated hydrogen chloride gas with water, finish adding acrylic acid dropwise in about 1 hour, add After completion, slowly raise the temperature to 180°C, apply a vacuum of 0.3 atmospheres, and keep steady to distill methacryloyl chloride to obtain 16.0 grams of methacryloyl chloride, and then high vacuum oil pump decompression distillation to obtain 32.7 grams of 2,4,6 - Trimethylbenzoyl chloride.
PUM
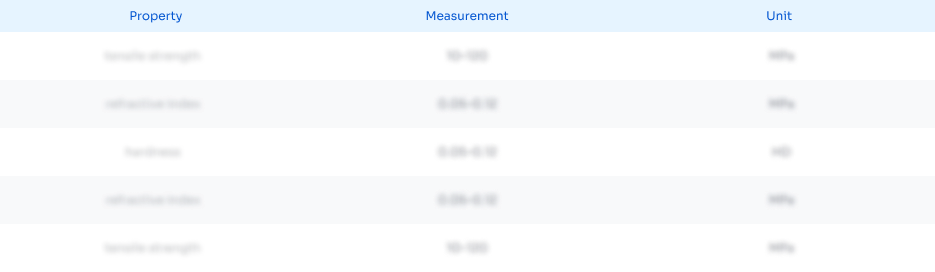
Abstract
Description
Claims
Application Information

- R&D Engineer
- R&D Manager
- IP Professional
- Industry Leading Data Capabilities
- Powerful AI technology
- Patent DNA Extraction
Browse by: Latest US Patents, China's latest patents, Technical Efficacy Thesaurus, Application Domain, Technology Topic, Popular Technical Reports.
© 2024 PatSnap. All rights reserved.Legal|Privacy policy|Modern Slavery Act Transparency Statement|Sitemap|About US| Contact US: help@patsnap.com